会员登录
MEMBER LOGIN
技术论坛
TECHNOLOGY FORUM
铸造行业“十二五”发展规划
发布时间:
2013-07-02 00:00
来源:
一、前言
铸造是装备制造业的基础,也是国民经济的基础产业。从汽车、机床,到航空、航天、国防以及人们的日常生活,如建筑五金、家用电器等都需要铸件。
2009 年5月,国务院颁布的《装备制造业调整和振兴规划》(以下简称《规划》)首次把大型铸件、关键铸件及基础配套件提升到与主机产品同等重要的战略高度。由先前的主机带动辅机发展变为一手抓主机,一手抓配套。我国装备制造业进入了主机与辅机必须同步发展的新阶段。《规划》明确提出,要提升大型铸锻件等配套产品的技术水平,夯实产业发展基础;要依托国家重点建设工程,大规模开展重大技术装备自主化工作;坚持自主开发与引进消化吸收相结合,通过加大技术改造投入,为发展大型核电、火电、水电、风电等高效清洁发电设备和钢铁、石化、船舶、轨道交通、机床、航空航天、汽车等产业提供大型铸件和高端关键铸件及各类功能铸件。
2010年10月,国务院颁布了《关于加快培育和发展战略性新兴产业的决定》,旨在将战略性新兴产业培育成为国民经济的先导产业和支柱产业。在所确定的节能环保产业、新一代信息技术产业、生物产业、高端装备制造产业、新能源产业、新材料产业、新能源汽车产业等七大新兴战略产业之中,“高端装备制造产业”位列其中。在当前国家大力加快培育和发展战略性新兴产业的形势下,抓住机遇发展高端装备制造业,对于推进行业产业结构升级和经济发展方式转变,提升装备制造业自主创新能力和国际竞争力,促进可持续发展,具有十分重要的意义。
“十二五”期间是我国经济转型的重要攻坚阶段,对于铸造业的发展更是一个关键期。认真贯彻国家“十二五”规划纲要精神,科学编制和有效实施铸造行业“十二五”规划,对于积极适应国内外发展新环境,加快促进我国铸造业由大变强,将起到有力的推动与促进作用。
二、我国铸造行业现状
(一)行业规模
1.铸件产量连续11年居世界首位
自2000年起我国铸件产量已连续11年居世界首位,在这11 年间,我国铸件产量以平均每年11%的速度增加(表1)。我国2010 年铸件总产量已达3,960 万t,产值约4,500亿元,铸造厂点约3 万家,从业人员约200 万人。从我国各主要行业的铸件消费量(表2)可见,2010 年汽车铸件比例已超过24%,已连续5年居各行业消费量之首。
表1 近11年来我国铸件产量增长情况
年 份 | 2000 | 2001 | 2002 | 2003 | 2004 | 2005 | 2006 | 2007 | 2008 | 2009 | 2010 |
铸件总产量 | 1,395 | 1,489 | 1,626 | 1,987 | 2,242 | 2,442 | 2,809 | 3,127 | 3,350 | 3,530 | 3,960 |
(万t) | |||||||||||
比上一年增长(%) | 10.3 | 6.7 | 9.2 | 22.2 | 12.8 | 8.9 | 15 | 11.3 | 7.1 | 5.4 | 12.2 |
注: 平均年增长率11%。
表2 我国各主要行业的铸件消费量
序号 | ![]() ![]() ![]() ![]() ![]() ![]() ![]()
|
2007 | 2008/2009 | 2010 | |||||||||||||
消耗量 | |||||||||||||||||
与比例 | |||||||||||||||||
行业名称 | 消费量(万t) | 占总产量的百分比(%) | 消费量 | 占总产量的百分比(%) | 消费量(万t) | 占总产量的百分比(%) | |||||||||||
(万t) | |||||||||||||||||
1 | 汽 车 | 570 | 18.2 | 620/730 | 18.2/20.7 | 960 | 24.2 | ||||||||||
2 | 内燃机、农机 | 430 | 13.75 | 460/510 | 13.7/14.4 | 570 | 14.4 | ||||||||||
3 | 矿冶、重机 | 430 | 13.75 | 440/450 | 13.1/12.8 | 490 | 12.4 | ||||||||||
4 | 铸管及管件 | 400 | 12.8 | 350/380 | 10.4/10.8 | 450 | 11.4 | ||||||||||
5 | 工程机械 | 350 | 11.2 | 310/350 | 9.3/9.9 | 390 | 9.8 | ||||||||||
6 | 机床、工具 | 200 | 6.4 | 330/280 | 9.9/7.9 | 330 | 8.3 | ||||||||||
7 | 轨道交通 | 150 | 4.8 | 170/180 | 5.1/5.1 | 220 | 5.6 | ||||||||||
8 | 发电及电力 | 150 | 4.8 | 170/190 | 5.1/5.4 | 200 | 5 | ||||||||||
9 | 船 舶 | 50 | 1.6 | 60/45 | 1.8/1.3 | 55 | 1.4 | ||||||||||
10 | 纺 织 | 40 | 1.3 | 40/30 | 1.2/0.8 | 35 | 0.9 | ||||||||||
11 | 其 它 | 357 | 11.4 | 410/385 | 12.2/10.9 | 260 | 6.6 | ||||||||||
合计 | 3,127 | 100 | 3,350/3,530 | 100/100 | 3,960 | 100 |
2.铸件进出口企稳回升
我国每年铸件出口总量占铸件总产量的8%左右(此数字仅是单纯的铸件出口,而未包括经加工组装在整机中的铸件量)。原来一些需要进口的铸件,如大型水电设备的转轮铸件、汽轮机缸体铸件、汽车发动机铸件等,现在我国可以制造,替代进口。只有极少数高端铸件需要进口(如飞机发动机耐高温单晶叶片、核电设备中的关键铸件)。铸件的进口数量,占我国铸件出口量不足1.5%,见表3。受2008年世界经济危机影响,我国铸件进出口显现较大的衰退,经2009年探底企稳后2010年呈恢复性增长。
表3 2006~2010年我国铸件生产及进出口状况 (单位:万t)
年份 | 2006 | 2007 | 2008 | 2009 | 2010 |
铸件产量 | 2,809 | 3,127 | 3,350 | 3,530 | 3,960 |
其中出口量 | 260 | 277 | 223.3 | 163 | 202 |
进口量 | 1.7 | 3 | 3.2 | 2.2 | 3.4 |
3.企业规模逐步增大
表4所示为2008年世界前十大铸件生产国家企业总数及企业的平均产量,从中可见,我国铸造企业数量比世界其他国家铸造企业的总和还要多,但企业的平均产量仅1,117t,远低于发达国家(如德国为9,640 t),甚至低于一些发展中国家(如巴西、印度)。这种状态正在渐渐改善,企业的平均产量2009年为1177t,2010年为1320 t,我国铸造企业的平均规模正逐步增大。
表4 2008年世界前十大铸件生产国家企业总数及企业平均产量
国家 | 中国 | 美国 | 俄罗斯 | 印度 | 德国 | 日本 | 巴西 | 意大利 | 法国 | 韩国 |
企业总数 | 30,000 | 2,170 | 1,650 | 4,700 | 600 | 1,702 | 1,340 | 1,167 | 479 | 873 |
(家) | ||||||||||
平均每家 | 1,117 | 4,970 | 4,727 | 1,455 | 9,640 | 3,322 | 2,504 | 2,260 | 4,985 | 2,366 |
企业产量 | ||||||||||
(t) |
(二)近年来我国铸造业的进步
1.铸件质量明显提高
一是铸件(特别是内燃机缸体、缸盖等复杂铸件)内、外废品率有了明显下降(先进企业缸体废品率已降至1.5%以下);二是某些类别铸件的尺寸精度、表面粗糙度、材质力学性能和耐热、耐蚀、抗磨等重要质量指标达到了国际一流水平;三是出口铸件的技术档次、质量、品种和数量都有大幅度提高,某些原来依靠进口的重要铸件已实现国产化。
近年来,我国重点骨干及部分中小铸造企业依据ISO 9001标准(汽车铸件生产厂依据更为严格的ISO/TS16949标准)建立起与国际接轨的质量管理体系(QMS),通过严格控制整个铸件产品实现过程确保铸件质量的稳定性和一致性。
由于球墨铸铁、等温淬火球墨铸铁(ADI)和蠕墨铸铁能够满足更高的综合性能(如低温韧性、高强韧性)要求,所以近年来得到进一步应用,我国球墨铸铁件所占比例已经接近世界平均水平;高性能铝合金、镁合金等有色合金铸件在制造业上也得到广泛的应用。
2.铸造企业技术水平有较大提高
近十年来,采用砂型铸造工艺的许多企业正向机械化、自动化方向迈进,传统的单一手工砂型铸造占据大半江山的局面得到了较大的改变。已有近千套的自硬树脂砂设备用于生产单件小批的中、大型铸件。数以千计的铸造企业都已使用感应电炉或冲天炉—感应电炉双联工艺。这些工艺手段使我国有能力生产各种类型的铸件,至今我国生产的最大球墨铸铁机床单体铸件为145t,最大的铸钢件为520t;已有100余家能生产单件重30t以上的铸件。
国内已有一批铸造企业在规模和技术水平上接近和达到世界一流企业水平。这些企业积极参与国家重大技术装备关键零部件的研制、生产,成为核电、水电、风电、超临界/超超临界火电、大型发动机缸体/缸盖等装备国产化自主制造的重要力量,并在国际竞争中取得明显优势。
3.铸造用原辅材料商品化程度大幅度提高
近年来,铸造用原辅材料的生产和供应已成为一个单独的产业。国内一些大型铸造原辅材料生产企业不仅在国内有举足轻重的地位,同时也向其它国家出口。优质的产品加之良好的服务,彻底改变了以前铸造企业使用原辅材料必须样样自备的局面,在提高铸件质量的同时又降低了生产成本。
4.国产铸造设备占有率和模具的制造水平有显著提高
我国铸件的巨大市场,促使国外许多知名的混砂、造型、制芯、熔炼、清理、检测设备公司在我国设点生产。国内原有的铸造设备制造厂加上一批新兴的公司通过技术引进、消化吸收、自主创新的方式,生产了许多性价比高的铸造装备, 基本满足了国内高端铸件生产企业需求,同时出口量呈逐年增加的态势。
铸造模具制造业也得到快速发展,长期困扰模具制造的“瓶颈”已基本解决。浙江象山、江苏无锡等地已成为我国铸造模具的制造中心。如发动机缸体、缸盖等复杂铸件的模具在国内均可制造。
5.铸造企业的专业化水平进一步提升
近年来,不少铸造企业加快了专业化步伐,致力于开发高技术含量、自主技术绝窍的产品。具有自己特色,并形成了一批以高紧实度造型+先进制芯+双联熔炼的发动机铸件铸造企业,一批以机械化为主的刹车毂、制动盘、排气管汽车铸件铸造厂,多家离心球墨铸铁铸管厂和离心下水铸管厂,以呋喃树脂自硬砂为主体的机床、箱体铸件生产厂、风电铸件厂和大型铸件生产厂,以V法为主体的铸造厂,以金属型或覆砂金属型为主的曲轴、磨球生产厂,以硅溶胶或硅酸乙脂为粘结剂的高档精铸件厂和以水玻璃为粘结剂的普通铸钢件精铸厂,有色合金铸件按零件要求组成了压铸厂、重力金属型厂和其它特种铸造厂等。专业化生产优越性得到了体现。
6.“绿色铸造”理念得到强化
近年来,节能减排、健康、安全等“绿色铸造”理念在铸造行业日益得到强化。
各级铸造行业组织多次利用业界高层论坛、学术交流、网刊等方式宣传节能减排、安全生产的重要意义。多项相关国家、行业标准及指导性文件已经颁布或正在积极制订中。国家工业和信息化部委托制定的《铸造行业准入条件》,把节能减排、达标排放、加强职业健康安全管理和劳动保护作为《铸造行业准入条件》的重要内容。
一些铸造企业,积极实施“6S”管理,大力加强企业文化建设,建设花园式工厂,在环境/职业健康安全管理方面与国际接轨,并依据认证标准及我国法规要求,在清洁生产、节能降耗、达标排放、杜绝重大事故和减轻职业危害等方面取得了显著成效。
7.产业集聚速度加快
近几年来,许多地方政府正在积极进行铸造产业集群(工业园)的建设,使铸造行业开始步入铸造零部件专业化、规模化的良性运行轨道。一些地方开始按资源、能源和产业优势进行企业兼并重组与整合,走铸造生产专业化的道路。结合铸造产业的梯度转移,使铸造企业分布更集中,布局更合理。我国各地已经建成和正在建设一批特色铸造产业集群、产业基地和工业园区。如安徽省宁国“中国耐磨铸件之都”、广东省高要“中国压铸产业集群示范基地”、河北省泊头“中国铸造之乡”、湖南省嘉禾“中国铸造产业集群试点县”等。
(三)我国铸造业存在的问题
1.铸件质量总体水平较低
多数铸造企业铸件废品率仍成倍高于发达国家(2%~3%)的水平。对个别质量和工艺要求特别高的关键铸件,我国还须进口。
2.铸造企业工艺装备的总体水平落后于发达国家
以大批量生产的铸铁厂为例,国外采用自动造型线、热风冲天炉—电炉双联熔炼、现代制芯中心等生产装备及热分析仪、真空直读光谱仪等先进检测设备,我国只有少数企业可与之相比,大部分企业仍相差甚远。
3.铸件生产的能耗、污染物排放较高,资源综合利用率较低
我国铸件生产的能耗是工业发达国家同类工艺的1.5~2倍。多数铸造企业的冲天炉炉气及铸造过程中的余热没有处理和利用。相当多的中小企业生产工艺落后,清洁生产的装备、原辅材料普及率不高,污染物排放量大,且没有配备有效的末端治理设施(有的企业虽有治理设施,但没有得到有效利用)。我国吨铸件的各种污染物排放总量是工业发达国家的3~5倍。
相当多的铸造企业没有配备有效的旧砂再生回用设施,大量废砂、废渣作为一般垃圾处理,资源的综合利用率较低。
4.铸造企业数量过多,平均规模较小
铸造企业过多,平均规模太小,工艺水平落后,由此引发的劳动生产率低、资源有效利用率低下、污染治理难度增大、事故频发和市场恶性竞争等一系列问题。这一直困扰着我国铸造业的科学发展,必须下大力气加以解决。
5. 企业的管理水平相对较低
目前,国内多数中小企业管理粗放,有些属家族式管理;许多企业管理体系不健全,没有建立ISO 9001质量管理体系,即使在已建立QMS并通过认证的企业中,也存在走过场现象。生产过程中,大量的关键工序、特殊工序没有得到有效控制,致使生产的废品率、能耗、料耗高,产品质量低,造成资源、能源及人力浪费。
6.劳动保护及安全生产尚有较大差距
近年来,铸造企业的劳动保护和安全生产现状虽然有了明显改善,但由于相当多的中小企业工艺与装备水平落后,加上科学管理跟不上发展,致使这些企业的劳动条件恶劣、职业病及安全事故频发。
7.从业人员素质偏低
目前,众多中小铸造企业的经营者缺乏现代企业管理理念,实施粗放式经营。工人中大多文化程度偏低,又缺少必要的培训,使他们对铸件品质、生产秩序、工艺纪律、企业管理等了解甚少,难以达到现代生产对员工素质的要求。在不少铸造企业中,管理人员、技术人员匮乏的问题也较突出。
三、铸造行业发展趋势
(一)世界铸造发展趋势
1.产业不断向新兴市场国家转移
基于不断变化的世界经济格局及国际分工的衍变,铸造产业同样存在世界范围内的梯度转移,出现并不断发展着由发达地区向欠发达地区转移的趋势。
2.技术向优质可靠、高效智能、绿色低碳发展
当前,世界铸造技术的发展趋势主要表现在以下三个方面。
1)优质
随着对机械装备性能、质量要求的日益提高,对铸件品质的高标准要求也不断提升。从铸钢、铸铁到铝镁等轻金属铸件,人们越来越重视采用金属液净化技术和设备。复合材料、轻金属的半固态铸造已开始应用于铸件生产,并向近净型发展。铸造企业已经越来越多采用X光、γ射线透视和CT扫描检测技术,在线检测技术也越来越受到重视,以确保铸件使用过程中的安全、可靠性。
2)高效
铸造企业的机械化、智能化水平日益提高,尤其是机器人、快速成型技术在铸造企业生产中的普遍应用,大大提高了企业的劳动生产率。实现了全系统CAD/CAM/CAE、网络技术、物联网技术、传感-检测技术等计算机技术的应用,大大提高了企业技术管理和生产管理效率。
3)绿色
工业发达国家十分重视开发新的节能、节材、清洁、低排放、低污染的铸造材料,生产全过程以低碳技术暨循环经济的“4R”为行业准则(减量化、再利用、再循环、再制造)来开展工作。
(二)“十二五”期间我国铸造行业发展趋势
1.铸件总产量持续平稳增长
我国铸件的人均用量与发达国家相比还有相当差距,国民经济各个领域对铸件仍将保持旺盛的需求,同时,铸件的出口也将不断增加,因此,“十二五”期间我国铸件总产量将随着国民经济增长而保持平稳同步增长。
2.技术研发能力显著增强
随着装备制造业的发展和各行业对铸件品质要求的提高,各铸造企业为了自身的生存与发展必须加大技术研发的投入,以提高企业的技术水平、装备水平、自主创新能力。因此,在“十二五”期间,必将促进我国铸造业技术研发能力显著增强。
3.产品与产业结构调整力度加大
为实现经济增长方式的转变,铸造行业必将加大产品与产业结构调整的力度,并通过“铸造行业准入条件”的推行和在铸造产业集群(铸造工业园)的建设中,对企业实行整合、兼并、重组、淘汰落后,从而加快铸造行业步入良性发展轨道。
4.环境保护与劳动安全明显改观
“十二五”期间,铸造行业在降低能耗、提高铸件成品率、污染物达标排放、废弃物及余热回收利用、改善作业环境、工伤及职业危害显著降低等方面会取得越来越大的进展,环境保护与劳动安全将有显著改观。
5.人才培养工作得到进一步加强
铸造人才问题已引起政府、行业和企业的广泛重视。随着铸造行业教育培训体系的建立和完善,通过各种渠道加强对铸造管理人才、技术人才和生产工人的培训,“十二五”期间,铸造专业技术人才匮乏、员工素质偏低的境况将获得明显改观。
四、“十二五”期间我国铸造行业发展战略、发展目标、主要任务
(一)指导思想
1.坚持把铸造产业结构战略性调整作为加快转变发展方式的主攻方向
“十二五”期间,要按走新型工业化发展道路的要求,加快向节约、集约发展方式转变,把铸造产业结构战略性调整作为加快转变发展方式的主攻方向,加大技术改造、自主创新、整合/兼并/重组和淘汰落后的力度,着力推进铸造产业结构的调整和优化升级。
2.坚持把技术进步与创新作为加快转变发展方式的重要支撑
“十二五”期间,铸造企业要把科技进步和自主创新作为加快转变经济增长方式的重要支撑;加快建立以企业为主体、市场为导向、“产、学、研、用”相结合的技术创新联盟体系,使企业真正成为研发投入和自主创新的主体。
3.坚持把推进节能减排、绿色铸造作为加快转变发展方式的重要着力点
“十二五”期间,铸造企业必须按照国家关于建设资源节约型、环境友好型社会的要求,把推进节能减排、绿色铸造作为加快转变发展方式的重要着力点,加强能源、资源节约和综合利用、强化生态环境保护,逐步淘汰、改造落后设备和工艺,不断提高工艺技术水平和铸件品质,走质量效益型、环境友好型的循环经济发展之路。
4.坚持把深化企业改革和管理创新作为加快转变发展方式的强大动力
“十二五”期间,要把深化企业改革和管理创新作为加快转变发展方式的强大动力,培育一批具有国际竞争力的企业集团,提高规模经济和产业集中度。培育一批产业联盟体,促进形成区域协调发展新格局。引导中小企业走“专、精、特、新”道路,提高市场竞争力。积极拓展国际合作与交流渠道,有效实施“走出去”战略,探索新的合资、合作方式,充分利用国际国内两个市场、两种资源。
(二)发展战略
1. 精品战略
要把我国由铸造大国变成铸造强国,提高铸件质量是关键。“十二五”期间,要把提高铸件质量摆在首位,瞄准世界先进水平,把为国民经济各行业提供优质铸件尤其是急需的关键铸件作为战略目标,增强企业新产品开发能力和品牌意识。鼓励铸造企业加大技术改造力度,提高机械化、自动化和专业化水平,不断开发新产品,提高新技术对产值的贡献度。
2. 绿色铸造战略
开发、应用低碳技术,在节约资源方面,要做到减量化、再利用、再循环、再制造。减少铸件废品、降低能源消耗。重视人的尊严、改善劳动条件、有效治理有害物质排放,提高铸造废弃物的综合利用。制定绿色铸造企业的行业标准,培育一批不同类型绿色铸造企业的典型,大力宣传、以发挥他们的示范引领作用,进而推进循环经济和清洁生产在铸造业的发展。
3. 结构优化战略
1)产业与产品结构调整
当前,在国家大力加快培育和发展战略性新兴产业的形势下,抓住发展高端装备制造业机遇, 在“十二五”期间,要重点在保增长中加快产业结构的优化调整。大力支持铸造骨干企业跨行业、跨地区、跨所有制的联合、兼并、重组,培育一批具有国际竞争力的科工贸一体化大型企业集团和“专、精、特、新”专业化生产企业,形成优势互补、协调发展的产业新格局。在抓紧进行行业结构调整的同时,铸造企业要做好企业内部的产品和产业结构调整。对尚需进口的关键铸件要实现技术突破,加快国产化步伐。要提高出口铸件的档次和附加值,以提高企业的竞争力。
在产品和产业结构调整过程中,引导企业准确把握市场发展方向, 防止盲目扩张、低水平重复建设和市场已饱和铸件的跟风建设,避免产能过剩带来新的损失。
2)准入制度与行业自律
要从根本上改变我国铸造行业的落后局面,一是靠市场竞争,二是靠政策导向。实施我国铸造行业“准入制度”是重要的手段之一。关闭浪费资源、污染环境和不具备安全生产条件的企业,使铸造行业健康有序地发展。
加强以诚信为核心的行业自律和以生产安全为准则的行业预警机制。推进铸造行业信用等级评价工作,组织制定行规、行约并监督实施,形成有力度的管理约束机制。
3)产业集群与铸造工业园区建设
要遵循新型工业化发展原则和国家相关产业政策,按市场经济规律和政策导向,对已具备产业集群雏形的产业集聚区和已建立的产业集群,要加强培育,坚持标准,按产业集群模式运作,培育各种产业集群的样板,总结经验,进行推广,以起到引领和示范作用。
随着国家开发中西部策略的进一步推进,铸造行业向中西部转移的趋势将越来越明显。在这个进程中,应加强必要的引导,增强新建、扩建企业的创新意识、尤其是环保意识。
4. 自主创新战略
技术改造、技术进步和自主创新是振兴铸造产业的核心,要着力抓好技术改造、技术进步和自主创新工作,完善科技创新体制,推动铸造业的内涵式发展。
要进一步加强企业创新平台建设,并逐步加大科研投入。加强以企业为主体的“产学研用”结合,并形成产业联盟。进一步加强国家标准、行业标准的制、修订工作,继续提高和国际标准相关联的采编率。“十二五”期间,还应逐步取得对新制订和修订的国际标准话语权、主导权,以提升我国的铸造标准化水平。
5. 人才战略
人才问题已经成为制约铸造行业发展的瓶颈。铸造企业应积极采取各种措施加以解决,各级行业组织要积极配合,广开企业人才培养的渠道。其中包括,加强行业教育培训体系建设,积极推进教育资源共享、人才交流合作,构建布局合理、分工明确、突出特色、保证质量、管理科学的社会化教育培训网络。充实和完善培训条件,提高培训质量。鼓励社会力量开展铸造人才培训。尽快建立“铸造工程师”、“铸造管理师”、“铸造技师”资格认证等职称认证体系。
(三)发展目标
1. 保持经济规模稳步增长,基本实现向质量效益型转变
铸件总产量:铸件总产量按年均增长6%计,到2015年达到5,000万t以上,年销售收入达到7,500亿元以上。
各主要行业的铸件消费量目标,见表5。
表5 各主要行业的铸件目标消费量
序号 | ![]() ![]() ![]() ![]()
|
2009年/2010年 | 2015年 | |||||||||||||||||
消耗量 | ||||||||||||||||||||
与比例 | ||||||||||||||||||||
行业名称 | 消费量 | 占总产量的百分比(%) | 消费量 | 占总产量的百分比(%) | ||||||||||||||||
(万t) | (万t) | |||||||||||||||||||
1 | 汽车 | 730/960 | 20.7/24.2 | 1,800 | 36 | |||||||||||||||
2 | 内燃机、农机 | 510/570 | 14.4/14.4 | 620 | 12.4 | |||||||||||||||
3 | 矿冶、重机 | 450/490 | 12.7/12.4 | 500 | 10.0 | |||||||||||||||
4 | 铸管及管件 | 380/450 | 10.8/11.4 | 500 | 10.0 | |||||||||||||||
5 | 工程机械 | 350/390 | 9.9/9.8 | 450 | 9.0 | |||||||||||||||
6 | 机床、工具 | 280/330 | 7.9/8.3 | 310 | 6.2 | |||||||||||||||
7 | 轨道交通 | 180/220 | 5.1/5.6 | 250 | 5.0 | |||||||||||||||
8 | 发电及电力 | 190/200 | 5.4/5.0 | 260 | 5.2 | |||||||||||||||
9 | 船舶 | 45/55 | 1.3/1.4 | 60 | 1.2 | |||||||||||||||
10 | 纺织 | 30/35 | 0.8/0.9 | 40 | 0.8 | |||||||||||||||
11 | 其它 | 385/260 | 10.9/6.6 | 210 | 4.2 | |||||||||||||||
合计 | 3,530/3,960 | 100/100 | 5,000 | 100 |
企业数量:到2015年,铸造企业数量将从目前3万家减少到2万家左右;力求到2020年再减少1万家左右,最终企业数量控制在1万家以内。
企业平均规模:到2015年,从2010年的1, 320t/家增加到2,500t/家。
2. 提升高性能铸造合金应用比例
到2015年,球墨铸铁铸件所占比例将达到30%以上;有色合金铸件所占比例增加到20%左右。
3. 攻克大型、高端、关键件铸造技术
1)解决大型及关键设备零部件(如:大型水电、火电、风电、核电以及船舶等设备的关键铸件)的铸造技术,实现国产化率达95%以上。
2)实现轨道车辆、汽车和3C产品铝、镁轻合金及特种合金等大型、复杂、高精度及特种功能铸件的批量生产。
4. 节能减排再上新台阶
1)大幅度降低铸造能源消耗,30%企业达到工业中等发达国家水平。
2)铸造企业的固废、液废及废气排放达到国家标准或地方标准。
3)在“十一五”基础上,单位产量能耗降低20%,单位产量排污降低15%。
4)旧砂再生回用率达90%以上。
5) 35%铸造企业达到《铸造行业清洁生产标准》。
铸造行业节能减排目标,见表6。
表6 “十二五”期间铸造行业节能减排目标
时间 | “十一五” | “十二五” | 2015年 |
期间 | 目标 | 测算 | |
能耗(吨标煤/吨合格铸件) | 0.6 | 0.48 | 减少0.12 |
排放(吨二氧化碳/吨合格铸件) | 2.3 | 1.84 | 减少0.46 |
(四)主要任务
1. 加快产业结构优化调整,增强企业竞争力
1)继续保持铸造生产可持续、稳定增长,与国民经济发展同步
加快产业梯度转移—由发达地区向欠发达地区转移、由东部地区向中部和西部转移,保持发展的基本平衡。形成集科研开发、产业链延伸、信息化建设、设备供应、技术服务等为一体的产业体系,产业体系更加完善,产业综合竞争力显著提高,满足我国装备制造业战略发展的需求。
2)在推行“铸造企业准入条件”试点的基础上,进一步完善铸造行业准入制度
加快产业结构优化调整,通过整合、兼并、重组等措施和政策引导,限制盲目扩张、重复建设,避免产能的严重过剩。有计划、有步骤地淘汰落后的铸造企业,切实提高企业生产规模、减少企业数量,实现规划目标。
3)实施“百千万工程”
支持大型铸造企业跨行业、跨地区、跨所有制的联合、兼并、重组,打造“百家”具有国际竞争力的科工贸一体化集团——综合百强;培育“千家”具有“专、精、特、新”优势的重点骨干企业,形成资源共享、市场互补,走专业化发展道路;引导“万家”企业按“准入条件”要求运作。“十二五“期间,使铸造行业形成健康、协调可持续发展的产业新格局。
4)加速推进铸造产业集群(铸造工业园)建设
“十二五”期间基本完成全国铸造产业集群体系建设和创新发展示范基地建设。在目前近300个铸造集聚区(工业园)基础上,重点培育50个特色铸造产业集群(工业园)和 10个示范铸造产业集群(工业园),在有条件的地区推广铸造“短流程”工艺,实现高炉铁液、电解铝液集中配送热装调质,直接浇注铸件的生产模式。
5)积极培育铸造行业示范工程
在自主创新企业、标杆铸造企业、节能减排、铸造产业集群、两化融合、铸造行业企业信用评价、教育培训、社会责任等方面,重点培育试点企业和示范区,树立不同类型的样板。
进一步完善铸造行业示范工程的评选、建设标准、运作模式、管理机制等相关文件。
6)提高产品附加值
引导企业延伸产业链,开发中高档产品,提高产品附加值, 发展现代制造服务业,增强产业园区综合配套能力。
2. 积极采用先进铸造技术与工艺装备
未来铸造技术的发展重点是向大型化、轻量化、精确化、智能化、数字化、网络化及清洁化的方向发展。在“十二五”期间加大铸造共性基础技术研究、积极采用先进铸造技术和装备,并加大推广力度。
1)重点研究与采用、推广的先进铸造技术
“十二五”期间,重点研究与采用、推广的先进铸造技术包括共性技术研究和关键件铸造技术两大方面,见表7、表8。
表7 共性技术研究
序号 | 分 类 | 内 容 |
1 | 新技术研发 | 单晶体铸件铸造技术; |
复合材料铸造技术: | ||
半固态铸造技术; | ||
高温、高强度、轻质合金高精度铸造技术; | ||
快速无模砂型铸造技术研究与开发。 | ||
2 | 铝、镁、钛等特种合金铸造技术 | 铝、镁、钛金属液熔炼; |
高性能的耐热、耐蚀、耐磨特种材质铸件研究与应用。 | ||
3 | 铸件缺陷及质量检测技术 | 无损检测技术、在线检测设备开发与应用。 |
4 | 旧砂再生技术 | 旧砂(粘土砂、水玻璃砂与树脂砂)再生技术、设备开发与应用。 |
5 | 绿色原辅材料应用技术 | 无污染、少污染的铸造原辅材料开发与应用; |
特种球化剂、孕育剂及处理工艺。 | ||
6 | 高效节能环保铸造工艺技术 | 造型、制芯、砂处理、熔炼、清理、环保设备开发与应用。 |
7 | 数值模拟及信息化技术 | 计算机辅助设计(CAD)与制造(CAM)技术。 |
高精度工艺过程数值模拟(CAE)技术。 | ||
工艺优化与铸件再设计技术; | ||
企业资源管理(ERP)技术。 | ||
8 | 金属液净化与预处理技术 | 金属液净化技术开发与应用,金属液过滤技术; |
金属液预处理(脱硫、变质处理等)技术。 |
表8 关键件铸造技术
序号 | 分 类 | 内 容 |
1 | 关键基础零部件 | 高性能汽车铸件:缸体、缸盖、曲轴等; |
蠕墨铸铁、等温淬火球铁(ADI)、非铁合金铸件等 。 | ||
床身等机床铸件; | ||
大型船用动力装置、曲轴、螺旋桨等铸件; | ||
海洋工程装备铸件等; | ||
高压柱塞泵、马达、液压阀、液压缸、液力变速箱、大功率液压偶合器等铸件。 | ||
2 | 能源类 | 百万千瓦级二代加、三代核电机组大型铸件的研究与开发,重点发展百万千瓦及以上核电设备铸件,百万千瓦及以上超临界/超超临界火电机组铸件。 |
70万kW及以上等级大型混流式水轮机组用铸件的研究与开发;,70万kW以上大型混流式水轮机组铸件,大型抽水蓄能、大型潮汐发电水轮机组铸件 。 | ||
200MW以上燃气轮机铸件。 | ||
5MW及以上风电机组系列铸件。 | ||
3 | 矿冶重机、石化 | 3300mm以上宽厚板支承辊、大型复合轧辊, 冷热连轧机铸件;单重为100t及以上石油、冶金、采矿、化工等铸件; |
大吨位铸锭。 | ||
4 | 航空航天、军工 | 航空航天、军工等铝、镁、钛合金铸件; |
大推力飞机涡轮机高温合金叶片、重型燃气轮机叶片。 |
2)优先发展的重大技术装备
为保证我国铸造行业由大做强,必须建立造型、制芯、砂处理设备、熔炼设备、浇注设备、除尘环保设备和铸造检测设备等在内的龙头企业产业集群。
“十二五”铸造行业应优先发展的重大技术装备,见表9。
表9 优先发展的重大技术装备
序号 | 设备名称 |
1 | 机器人-自动化制芯中心。 |
2 | 高紧实度粘土砂高效自动造型生产线。 |
3 | 无粘结剂砂型(V法造型/消失模铸造)造型线。 |
4 | 大功率高效粘土砂砂处理系统。 |
5 | 大型自硬砂连续式混砂机。 |
6 | 粘土湿型砂在线检测装置。 |
7 | 旧砂(粘土砂、水玻璃砂与树脂砂)再生成套设备。 |
8 | 内燃机缸体缸盖铸件专用抛丸设备。 |
9 | 大吨位振动落砂机。 |
10 | 大型一拖二、一拖三大功率中频感应加热电源。 |
11 | 大吨位电弧炉及炉外精炼设备。 |
12 | 大吨位外热风长炉龄冲天炉,冲天炉专用除尘设备。 |
13 | 大吨位压铸机铸造单元。 |
14 | 自动化磨削清理装置。 |
15 | 铸件频谱谐波振动消除应力装置。 |
16 | 铸件质量在线无损检测装置。 |
3. 加强基础能力建设和自主创新建设
1)加大企业技术改造力度,提高企业工艺和装备水平
支持企业技术改造,提高工艺、技术和装备水平,淘汰“高污染、高消耗、低效率”等落后工艺和装备;支持企业进行节能降耗和资源综合利用改造,减少能源、材料消耗和污染物排放。
2) 加大企业自主研发力度,提高企业技术创新水平
鼓励大型、骨干铸造企业建立自己的技术中心、研发中心、博士后流动站,并依托这些平台开展研发工作。众多的中、小型企业,除了加强自己企业的研发能力外,可以通过与其它企业的联合,建立面向铸造工业园区或产业集群的开发联盟、检测中心和咨询服务等公共技术服务平台。
引导企业加大研发投入,提高研发经费在生产费用中的比重。优势企业的研发投入要达到销售收入的3%以上,一般企业的研发投入要达到销售收入的2%以上。发挥各类企业特别是中小企业的创新活力,鼓励技术革新和发明创造,逐步由模仿创新向自主创新发展。鼓励企业争创国家、省、市级高新技术企业,引导企业积极申报专利,积极申报国家、省、市级科技成果奖,激发企业通过自主创新,创建企业自主知识产权。
3)“产、学、研、用”结合,形成产业联盟
鼓励铸造企业与相关上下游企业、大学、研究院所等建立研发合作产业联盟。各自发挥长处,不断提升企业的研发能力,共同解决企业需攻关和开发的课题,并争取国家级重大攻关课题,实现铸造行业的整体发展。
4)完善标准体系,加快标准贯彻实施
在“十一五”的基础上,继续加快铸造标准的制、修订工作,适时推出行业组织标准,不断补充完善行业标准。与国际标准相关联的铸铁标准的采标率应达到92%以上,与国际标准相关联的铸钢标准的采标率应达到95%以上。
4. 全面提升企业管理水平
积极引导铸造企业引入现代企业管理理念和模式,在人力资源管理、市场营销管理、质量管理、品牌管理、创业管理等方面结合本企业实际,进行探索、实践,正确处理好对内关系和对外关系,以提高企业核心竞争力。
认真总结和推广企业在加强企业文化、战略规划、教育培训、奖惩制度等方面建设的经验。
促进企业认真搞好管理体系建设,全面提升企业科学规范化管理水平。“十二五”期间铸造企业应有30%以上通过ISO 9001质量管理体系认证;15%以上企业通过ISO 14001环境管理体系认证;5%以上企业通过OHSAS 18001职业健康安全管理体系认证。
5. 推广节能减排技术
在铸造行业内积极开展替代技术、减量技术、再利用技术、资源化技术、系统化技术等关键技术研究,突破制约循环经济发展的技术瓶颈,认真做好节能节材、减少各种废弃物排放技术的应用与推广,适时启动铸造企业能源效率评价工作。鼓励使用先进工艺装备和产品,限制并逐步淘汰落后工艺装备和产品,依据工业和信息化部定期下达的产业结构调整指导目录,积极认真加以落实。
1)制定相关政策和法规
一方面限制污染和排放,另一方面鼓励企业积极实施治理。
2)施行“排污者付费原则”
谁造成环境污染,谁就必须承担环境伤害的责任。
3)建立处理工艺和程序,在源头上减少使用原材料及产生废料
推广铸件生产全过程封闭输送;应用供风排风的平衡原理,科学合理地组织厂房内空气流动,以获得良好稳定作业环境;不断完善铸造旧砂再生技术。
6.推进“两化融合”
“两化融合”即工业化与信息化融合。诞生于“十六大”的“以信息化带动工业化,以工业化促进信息化”论断,到“十七大”,进一步上升为“促进信息化与工业化融合,走新型工业化道路”。
在铸造行业中推动“两化融合”工作的开展,应以设计研发信息化、生产装备数字化、生产过程智能化和经营管理网络化为目标。
企业要从效益驱动、总体规划、分步实施和重点突破四个方面推进“两化融合”工作。重点突破企业信息化管理中的一些“瓶颈”环节,以提升企业核心竞争力。
政府及行业组织要从调查评估、示范推动和监测服务三个方面,积极推进铸造行业 “两化融合”工作的深入开展。
7.构建行业教育培训体系,加强人才队伍建设
1)充分发挥以企业为主体、高校及职业院校为基础,建立学校教育与企业培养紧密联系、政府推动与社会支持相互结合的行业人才培养体系。
2)制定培训基地资格认定标准,广泛吸引更多企业和社会力量进入铸造教育培训领域,完善教育培训基地管理和布局,着力选拔和培育一批铸造教育培训示范机构。
3)制定培训机构考核评估办法,加强对已认定的培训基地的监督和管理,努力提高培训质量。
4)搞好培训课程体系规划,加强施教体系建设,积极推进远程教育,增强行业教育培训覆盖率。
5)推动骨干企业开展培训,参与铸造产业集群调研,推进产业集群区域铸造教育培训工作,评选教育培训示范企业。
6)积极推进职业教育资格制度建设,认真开发铸造管理师、铸造工程师和铸造技师等培训认证工作,建立培训证书统一发放以及培训证书分类和换发制度。
7)加强国内协作,开展联合培训,拓展培训渠道,推动行业教育培训工作向高层次发展。
8.推动铸造领域双边及多边国际交流与合作
拓展与世界各国和地区铸造业组织的合作关系,互动互访,沟通信息。组织开展国际铸造业技术交流与经贸合作,为企业引进技术、科技人才和战略投资牵线搭桥。加快“走出去”步伐,帮助企业开拓国外市场,拓展高端铸件市场份额,深度参与国际竞争。
持续推进国际交流体系建设,以世界铸造论坛、世界铸造会议、亚洲铸造论坛、金砖四国铸造高层论坛、中国国际铸造博览会、铸造活动周等国际性活动为平台,加强与世界各国和地区铸造组织的合作及有效沟通,为企业在更高水平上参与国际竞争和国际合作提供机会。
提高国际贸易维权意识,维护铸造业产业安全,保护自主知识产权。多种途径减少、避免铸造产业国际贸易摩擦(如:两反一保障等)。
五、相关措施与政策
(一)积极争取和充分利用国家相关惠及政策
积极争取和充分利用国家的财政补贴、税收政策、金融政策、专项奖励等相关惠及政策。通过财政、税收、金融等各项政策的联合实施,大力推进铸造行业的重点领域和重点企业的发展。
1. 积极争取国家强化投融资支持力度
中央预算内投资支持符合条件的企业技术进步和技术改造项目,在此大环境下,铸造行业组织应积极争取国家继续对重点骨干铸造企业实行扶优扶强的政策,其中包括减税、扶持补贴、发展基金等支持铸造业发展的各项政策。引导设立股权或创业投资基金,积极推动企业利用知识产权等无形资产进行质押贷款,拓宽企业融资渠道。“十二五”期间,要积极发挥增值税转型政策对企业技术进步的促进作用,鼓励企业加大技术改造力度,加快装备更新,调整产品结构,推动企业技术进步。
2. 利用好国家科技创新基金
铸造行业组织要就行业中一些共性技术难题和亟待开发的技术、关键铸造设备等重大课题组织攻关,积极向政府有关部门争取经费和政策支持,如“中小企业创新基金”、“重大专项”、“863”、“节能减排改造补贴”等。
3. 认真落实《装备制造业技术进步和技术改造项目及产品目录》
支持使用国产首台(套)重大技术装备,支持“目录”内有关铸造方面的装备自主化、节能节材减排改造、企业兼并重组后内部资源整合、区域性四大基础工艺中心建设,鼓励、支持企业跨地区重组并购,加强产业资源整合,为发展现代制造服务业做出贡献。
(二)加快铸造行业淘汰落后产能,推进节能减排的进程
通过产业政策和专项治理行动,积极调整产业结构,促进铸造行业淘汰落后产能、节能减排工作。在产业政策上强化行业准入,以铸造行业节能减排作为行业结构调整这一首要任务的突破口。严格执行国家相关法令、法规,并依靠政府对铸造行业的调整、整合等政策引导和市场竞争的优胜劣汰,依法淘汰落后工艺技术、关闭破坏资源、污染环境和不具备安全生产条件的企业。
1. 支持“铸造企业准入条件”试点工作的实施,加速推进铸造产业集群建设和示范工程建设
通过实施“铸造企业准入条件” 试点工作,加快产业结构优化调整,通过整合、兼并、重组及淘汰落后产能等措施和政策引导,限制盲目扩张、重复建设,避免产能的严重过剩。
新建、扩建和改建铸造企业必须符合“准入条件”的规定。各级有关政府部门在对新建、扩建的铸造企业进行立项审批、土地供应、信贷融资等管理工作中要以“准入条件”为依据,对不符合“准入条件”的新建、扩建铸造企业,主管部门不予审批,工商行政管理部门不予发放营业执照,相关部门不予办理手续。不符合“准入条件”的铸造企业,应抓紧进行整改,在整改期限内,不能享受优惠政策,不能申报任何优惠项目。
加速推进铸造行业示范工程建设,重点培育铸造产业集群试点和示范区,树立不同类型的样板。
2. 制定行业能源及污染排放标准
在积极引导铸造企业认真贯彻执行国家颁布的通用能源及污染排放标准的基础上,铸造行业组织还应制定和修订铸造行业相关节能减排标准,进一步细化、量化,并具有可操作性。
借鉴国外治理废弃物排放经验,结合我国国情及铸造业实际情况,在有条件的地区开展工业企业向外排出废弃物资源治理费试点工作,以促进企业提高资源利用率,加大工业废物的回收再生利用,发展循环经济。
3. 完善职业健康安全管理体系
积极引导各级行业组织与国家、地方相应的职业健康与安全、环保部门建立密切的沟通、联系渠道,依托铸造行业准入条件的试点、贯彻、落实等具体工作,监督、规范、约束企业在职业健康安全、环境保护、节能减排方面的违规、违法行为。
(三)提升行业组织建设水平,充分发挥行业组织作用
“十二五”期间,铸造行业组织要以国务院办公厅发布的《关于加快推进行业协会商会改革和发展的若干意见》为指南,坚持改革发展的市场化方向,健全现代行业组织内部治理制度,建立和形成与市场经济相适应的行业组织发展格局,努力为经济社会发展服务。
1. 顺应时代进步和要求,努力为经济社会发展服务
坚持“四个服务”,即服务政府,协调和指导行业发展,落实中央经济政策,当好政府的参谋助手;服务行业,促进行业规范发展,为行业做强、做大提供有力支撑;服务会员,提供多元化服务,为企业科学、健康、可持续发展提供保证;服务社会,积极承担社会责任,在促进节能减排、加强劳动保护、实现低碳发展、构建行业诚信等方面发挥重要作用。
2. 健全现代行业组织内部治理制度,逐步完善以章程为核心的法人治理结构
健全会员(代表)大会、理事会、监事会等制度,做到民主选举、民主决策、民主管理、民主监督;建立诚信自律机制,鼓励行业组织建立服务承诺制度,向社会公开服务项目和标准,维护会员合法权益,接受社会和会员监督;促进行业组织人才队伍专业化、职业化、知识化、年轻化水平。争取到“十二五”末期,全国各级行业组织实现领导人自选、经费自筹、人员自聘、会务自主,基本实现内部制度健全、民主机制完善、法人治理结构清晰、职能作用发挥明显、普遍接受社会评估、从业人员素质显著提高的目标。
3. 建立和形成与市场经济相适应的行业组织发展格局
鼓励铸造产业集聚区、产业集群(工业园区)内的行业组织加强合作交流,形成区域行业组织优势,放大服务和自律效应;鼓励在具有产业、产品和市场优势的经济发达地区,尝试建立跨区域性的行业组织,形成新的行业组织发展模式;培育一批在国内外有广泛影响力的行业组织,形成层次不同、覆盖广泛、作用明显的行业组织发展格局。
4. 推进行业组织改革向市场化方向发展
要以改革的方式解决问题,坚持以市场为主体,遵循价值规律、供求规律、竞争规律等市场经济的基本规律,不断深化服务内涵,提高服务质量,提升服务效益。采取协商、协作、协同、协调的方法,公开、公平、公正处理行业事务;不断加强能力建设,不断拓展服务功能。积极承接政府管理职能逐步向行业组织的转移,加强行业自律,提升行业道德水准,推进行业诚信建设。更加注重社会公共利益和社会群体的合法权益,引导全行业关注民生,履行社会责任,开展公益事业。
附件下载:

-
地址:济南市解放路134号 电话:0531-86401781 / 86952422 传真:0531-86465075
邮箱:foundry-shandong@163.com 邮编:250013
版权所有 © 山东省铸造协会 鲁ICP备2021002429号
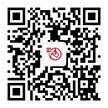
官方公众号