会员登录
MEMBER LOGIN
技术论坛
TECHNOLOGY FORUM
有关感应电炉熔炼铸造用钢的几个问题
发布时间:
2016-06-02 00:00
来源:
从 1899 年第一台用于熔炼合金的感应电炉问世,迄今还不到 120 年,在此期间,感应 电炉熔炼技术经历了一段应用不断扩大、设备不断改进的持续、交互发展过程,在许多方面 都有了惊人的发展:在电源方面,从工频电源供电到高频发电机供电,进而到由静态变频电 源供电;在炉型方面,从水平熔沟式熔炉到垂直熔沟式熔炉,进而到无芯的坩埚炉;在熔炼 的合金方面,从各种有色合金到铸铁,进而到不同的钢种,包括碳钢、各种低中合金钢、高 锰钢、不锈钢、耐热钢乃至镍基高温合金。 感应电炉的首创者应该是英国的 Ferranti,他提出的熔沟感应电炉设计方案,于 1887 年 获得了第一项专利。1899 年,瑞典的 Franklin kjellin 制成了第一台水平熔沟式工频感应电炉, 后来,美国的 J. Wyatt 对此进行了改进工作,1916 年,制成了第一台垂直熔沟式工频感应电 炉,用于熔炼黄铜之类的有色合金。 大约也就在 1916 年前后,美国的 Ajax Northrop 公司开发了由变频发电机供电的高频坩 埚式感应电炉。这项创新随即在美国得到了很快的发展,其应用很快就从熔炼有色合金到熔 炼铸铁,进而发展到炼钢。 1930 年前后,变频发电机供电的高频坩埚式感应电炉,在美、欧一些工业国家(包括 前苏联)得到了广泛的应用,很快就制造了容量 8t 的大型熔炼炉。 1930 年,美国 Pennsylvania 州 Lebanon 铸钢厂就有一台高频坩埚式感应电炉投入生产, 容量 2000 磅,熔炼的钢种有碳钢、低合金钢、CA-6NM 马氏体不锈钢和 CF3M 奥氏体不锈 钢。
1930 年,日本住友公司从美国 Ajax Electrothermic 公司购买了一台高频坩埚式感应电 炉(发动机功率 100kM,供电频率 960Hz),用于熔炼铜合金及其他有色合金,这可能是日 本第一台用于工业生产的感应电炉。1931 年,日本东京芝浦制作所从美国 Ajax Northrop 公 司购买了有关的专利技术,开始制造高频感应电炉。其后,日本的三菱电机公司也着手生产 中频感应电炉。在这种条件下,日本坩埚式感应电炉的应用发展很快,而且熔炼的合金品种 不断增多,包括各种对冶金质量有严格要求的钢种。
第二次世界大战以后,随着世界工业的发展,感应电炉熔炼技术也有了同步的发展:首 先是从发动机供电的高频坩埚式感应电炉发展到中频供电;同时又推出了静态频率倍增装 置,可使工频电源的频率增大到原来的 3 倍或 5 倍。从而增强了中频坩埚式感应电炉发展的 势头。 随后,又开始了工频坩埚式感应电炉推广应用的新局面。从 50 年代初开始,欧洲比较 广泛地将其用于熔炼铸铁,取代冲天炉。1970 年代,装设了一台容量 60t、功率 21MW 的工 频坩埚式感应电炉,可以认为,这一发展过程也就大致达到了顶峰。 70 年代中期,晶闸管静态变频中频电源问世,接着又开发了逆变变频及其控制技术, 频率转换效率从早先的 60~80%提高到 97~98%,坩埚式感应电炉的热效率可达到 70%, 充分显现了新型变频感应电炉的的优越性。 从 1980 年起,中频变频坩埚式感应电炉在世界各国的应用迅速扩展,很快就取代了坩 埚式工频感应电炉。目前,用于生产铸钢件最大的感应电炉,可能是奥钢联 Voest-Alpine 铸 造厂装设的容量 38t 的炉子,功率 16MW,频率 250Hz,是 ABP 公司的 IMF 系列产品。用 以生产涡轮机、压缩机和重型装备用的优质中、大型铸钢件。 钢铁行业采用感应电炉炼钢的也日渐增多。目前,印度 Viraj 制钢公司正在邻近孟买的 马哈拉施特拉邦的塔拉普尔工厂装设 3 台 IMF 型感应电炉,每台容量 30t,功率 18MW。 一、感应电炉在铸钢业界中的应用 从上世纪 30 年代开始,一些主要工业国家就都有用感应电炉炼钢的报道。早期,主要 用于熔模精密铸造,也生产少数小型铸钢件。 静态变频电源问世以后,随着变频设备的不断改善,感应电炉在各工业国家铸钢行业中 的应用进展很快:产品从一般的小型铸件逐步扩展到重要的中、大型铸件;熔炼的钢种也从 碳钢、低合金钢逐步扩展到高锰钢、工具钢、不锈钢、耐热钢以及各种高温合金。 在这种形势下,1986 年,美国铸造协会铸钢分会曾确立了一项关于发展感应电炉熔炼 的课题[1]。工作的第一阶段是回顾并分析有关的文献资料;工作的第二阶段是拟订一项推 荐性的“感应电炉炼钢作业规程”,并在承担这一课题的铸造厂进行有目标的实际作业试验, 从而对作业规程进行考核、评估。这项研究工作对感应电炉在铸钢行业中的应用是非常有益 的。 我国采用感应电炉炼钢起步较晚,可查阅到的文献资料也很少。有的书上提到:“我国 于 20 世纪 40 年代开始用感应电炉炼钢。”但是,迄今还未能查阅到具体的文献。 据我的一管之见,我国铸钢行业采用感应电炉熔炼大约起始于 50 年代后期。早期,基 本上都是用于熔模精密铸造,产量也很有限。70 年代末期实行改革开放政策以后,从 80 年 代起,铸造行业持续以惊人的速度发展,以感应电炉为熔炼设备、生产铸钢件的厂家日益增 多,工艺技术也不断有所改善。起初,只是用于生产质量要求一般的小型铸钢件,90 年代 以后,铸钢件产品的档次也逐步提高,现在已经可以生产各种优质的高合金钢铸件。 铸钢业界采用感应电炉作为熔炼设备,与用电弧炉熔炼相比,确有不少优点值得关注, 这也是其应用范围不断扩展的主要原因。但是,感应电炉熔炼也有不少必须正视的问题。铸 钢企业选用熔炼设备时,应该根据企业的具体条件、铸件产品的特点,从多方面作可行性分 析,不能简单地追逐潮流。
尽管奥钢联 Voest-Alpine 铸造厂已经用 38t 的炉子生产铸钢件,但是,考虑到耐火炉衬 和冶金质量方面的制约,我个人认为铸钢业界用的炉子还是 10t 以下的小型炉子为宜。在与 炉外精炼设备配合使用的条件下,才可以采用更大的炉型。 确定选用感应电炉后,还要按照产品的质量要求,选定炉衬制备方案、制订熔炼作业的 规程。 但是,我国铸钢业界在感应电炉熔炼方面的经验毕竟还是不多,据我所知,到目前为止, 未能掌握感应电炉熔炼要点的铸钢厂家仍然不少,有的是炉衬材料选用不当,有的是熔炼作 业不符合冶金要求。其中,不少企业不规范的程度已经越过了保证质量的底线,这种情况当 然会影响产品的质量和档次。特别要提出的是:在我国铸钢业界,感应电炉炼钢不加炉盖可 说是已成为常态,而这种作业方式是不能容忍的。首先是,由于辐射损失的热量多,导致炼 钢的能耗增加 10%以上。再就是,增强了钢液与大气的接触,对冶金质量的负面影响很大, 如:钢液氧化的程度增强;钢液自大气吸收的气体增多;合金元素的烧损增多、收得率不稳 定;钢中非金属夹杂物含量增多等等。 为了切实帮助企业掌握感应电炉炼钢的特点,切实做到在节能、降耗的基础上提高产品 的质量和档次,在采用感应电炉熔炼日益增多的今天,我觉得协会的铸钢分会有必要参照美 国协会铸钢分会的作法,建立一个课题组,编制推荐性的《感应电炉熔炼铸钢的工艺要点》。
二、感应电炉炼钢的长处和短处 近 30 年来,感应电炉在铸钢业界的应用发展很快,当然是由于其具有不少长处,但是, 另一方面,它也有很多短处。选用其作为熔炼设备,一定要进行全面的分析、研究,力求扬 其所长、避其所短,切不可凑热闹、赶潮流。设备选定以后,就应该对其特性有比较全面的 了解,力求在节能、减排的基础上不断提高铸件产品的质量。 以下,就感应电炉熔炼铸钢的长处和短处作简单的分析,供参考。
1、长处 在铸钢熔炼方面,与电弧炉熔炼相比,采用坩锅式感应电炉有不少长处,如: (1)感应电炉虽然也是高功率的耗电设备,但是对电网的干扰比电弧炉小得多;
(2)在对 环境的影响方面 熔炼过程中噪音小、排放的烟、气、粉尘和废渣都比较少; (3)在资源的利用方面 装炉材料(包括加入的各种合金元素)的烧损少、收得率较 高。造渣材料的用量小得多,而且不用电极;
(4)在冶金功能方面 由于有电磁搅拌作用,钢液的成分比较均匀,钢液的温度也比 较均匀,温度控制也比较方便,没有因电极而致的增碳问题。由于没有电弧的高温作用,也 没有氮在高温下离解而易于被钢液吸收的问题;
(5)设备的投资较少,占用场地的面积也比较小;
(6)较易于实现作业的自动化。
2、短处 由于具有上述长处,自从上世纪 80 年代以来,坩锅式感应电炉在铸钢方面的应用发展 很快,但是,坩锅式感应电炉也有其特有的短处,制约它的发展。‘如何避短?’是工艺技 术人员必需面对的课题。要避短,就应该对这些短处有充分的了解。 (1)耐火炉衬方面的问题 耐火炉衬是坩锅式感应电炉的重要组成部分,确保其正常运行,对设备作业的可靠性、 经济效益、安全性乃至铸钢产品的冶金质量都至关重要。 坩锅式感应电炉熔炼所用的能量,是由感应线圈产生的磁通量、通过耐火炉衬传送到炉 内金属的。耐火炉衬的厚度增大,则漏磁通增大,感应器输出的功率、功率因数和电效率都 随之降低。为了尽量减少平衡电容对无功功率的补偿、提高电效率,必需尽可能地使耐火炉 衬的厚度减到最小。因而,在炼钢用的各种熔炉中,感应电炉耐火炉衬的厚度,比任何炉型的炉衬都小得多,但是,其作业条件却又比其他炉型的炉衬苛刻得多。 1)炉衬的内表面接触熔融的钢液、温度很高,外表面则与水冷的感应线圈相接,薄薄 的炉衬中温度梯度却非常之大。 2)炉内的钢液因电磁作用而不断搅拌,增强了钢液对炉衬的冲涮,也增强了其中悬浮 的氧化物对炉衬的侵蚀,而且搅拌作用也使钢液吸收气体的可能性增大。 3)如果炉衬打结的紧实度不够,或烧结不好,熔炉过程中有钢液渗入炉衬的裂隙,渗 入的钢液因为有感应加热的作用,不会在裂隙中凝固,而要在裂隙中继续深入,直到接触线 圈、引起短路,甚至造成重大的安全事故。 因而,对炉衬耐火材料的性能、粒度级配、炉衬的修筑、炉衬的烧结都必须严格要求, 不能有丝毫马虎。
(2)冶金功能方面的问题 坩锅式感应电炉熔炼铸钢,其冶金功能比电弧炉熔炼差得多,因此,早期只能用于熔炼 冶金质量要求一般的钢种,制造小型铸钢件。上世纪 80 年代以后,随着设备和耐火材料的 不断改进,可以在熔炼过程中实施温和的氧化沸腾,增强其冶金功能,适用范围也逐步扩大 到优质低合金钢、高合金钢,乃至超低碳不锈钢和各种高温合金。但是,感应电炉熔炼在冶 金功能低的问题仍然不能忽视。
1)感应电炉熔炼,炉渣是靠钢液传导的热量使之熔化的,炉渣的温度低于钢液的温度, 不能像电弧炉熔炼那样,经由钢液-炉渣之间的多种冶金反应,实施氧化精炼和扩散脱氧。 2)电弧炉熔炼,熔池是浅盆型,渣线部位的直径大约是熔池深度的 4~5 倍;坩埚式感 应电炉熔炼,熔池是圆筒形,熔池的直径小于其深度,二者之比大约 0.6~0.75。由此可见, 感应电炉熔炼时,钢液-炉渣接触的界面比电弧炉熔炼时小得多,根本就不可能利用钢液炉渣之间的冶金反应进行冶炼作业。 因此,铸钢企业采用感应电炉熔炼时,对炉料的要求必须非常严格:各种原材料都要确 知其化学成分;装炉材料的用量都要由计算确定;废钢和回炉料都必须干燥、无泥沙、无油 污;装炉材料的最大尺寸不能大于坩埚内腔尺寸的 1/2。 三、炉衬 耐火材料炉衬,是坩埚式感应电炉重要组件,影响炉子的熔炼功能、钢的冶金质量,尤 其关键的是作业安全。由于坩埚式感应电炉适用于各种铸造合金的熔炼,如铸铁、铸钢、铜 合金、铝合金和锌合金等,小型感应电炉,炉衬可购买成型的预制坩埚。实际生产中用于铸 钢的坩埚式感应电炉,一般都由铸造厂根据熔炼合金的品种选购适用的耐火材料,自行修筑 炉衬,并做好烧结的作业。 1、炉衬用耐火材料的基本情况 常用于坩埚式感应电炉的几种耐火材料,基本成分和耐火性能见表 1。
表 1 几种常用耐火材料的基本成分和耐火性能 材料名称 硅砂 电熔镁砂 冶金镁砂 氧化铝质材料 镁铝尖晶石
化学成分(概略值)(%) SiO2≥95 MgO≥96 MgO≥88 Al2O3≥90 Al2O3﹕MgO(71.8﹕28.2)
耐火度(概略值) (℃) 1700 2300 2000 2000 2135
最高作业温度 (℃) 1550 1800 1700 1800 1900
2、适用于炼钢用炉的衬耐火材料 随着感应电炉在铸钢业界应用的发展,自上世纪 80 年代起,铝镁尖晶石型炉衬材料的 应用逐步受到重视,目前,各工业国家铸钢业界所用的坩埚式感应电炉,基本上都采用尖晶 石型炉衬。
近年来,我国也有一些铸钢企业采用了尖晶石型炉衬材料,其中,有些厂家是购买国外 厂商预配好的材料,虽然使用效果很好,但生产成本提高很多,而且对它的特性不甚了解。 在此,我主要是想介绍一些有关尖晶石型耐火炉衬的特性,供业界同仁自行配制炉衬材料、 进一步改进炉衬材料时参考。同时,鉴于目前硅砂炉衬、镁砂炉衬、氧化铝质炉衬在我国铸 钢业界还都有应用,也顺便对这些材料的特性作一点简单的介绍,供参考。
(1)硅砂炉衬 以硅砂为基本耐火材料修筑的炉衬,通常也称为酸性炉衬。硅砂的优点很多:首先是 是 资源丰富、价格低廉;而且以硅砂为基本耐火材料制成的坩埚,在接近其熔点的高温下仍具 有很好的强度,耐骤冷、骤热的性能好;特别应该提到的是,炉衬烧结过程中,硅砂的石英 相变膨胀能弥补烧结过程中的体积收缩,从而提高烧结层的致密度,降低炉衬烧结层中的孔 隙率。因此,各国铸造行业中,用于熔炼各种铸铁的坩埚式感应电炉都广泛采用以硅砂为基 础的炉衬材料。 但是,SiO2的耐火度低,基本上就不能适应炼钢温度。而且,SiO2在高温下的化学活性 很强,能与炼钢过程中的各种碱性氧化物乃至中性氧化物作用,例如,FeO 与硅砂接触后易 于生成熔点为 1205℃的铁橄榄石(Fe2SiO4),铁橄榄石还能进一步与 SiO2或 FeO 作用,生成 熔点为 1130℃的共晶组分。此外,SiO2 还可能被钢液中一些活性较强的元素还原。因此, 硅砂炉衬用于炼钢,既不能保证钢的冶金质量,也不能保证炉衬的寿命。从上世纪 80 年代 后期起,各工业国家用感应电炉生产铸钢件的铸造厂,就已经不用硅砂炉衬。据我所知,我 国迄今仍有一些企业采用硅砂炉衬熔炼铸钢,这种状况是亟待改进的。
(2)镁砂炉衬 常用的炉衬材料是 MgO 含量为 86%以上的冶金镁砂,是由菱镁矿经高温煅烧制成的。 如果将冶金镁砂置电弧炉中重熔,可使其中 SiO2、Fe2O3 等杂质的含量降低,得到纯度更高 (MgO 含量在 96%以上)的电熔镁砂。电熔镁砂多用于制作真空感应电炉的炉衬。 冶金镁砂的耐火度很高,是碱性电弧炼钢炉的常规炉衬材料,虽然其熔点很高,不容易 烧结,而且膨胀系数大,但是由于电弧炉的炉衬很厚,借助于加入大量的粘结材料、用湿法 打结,完全可以弥补这方面的不足。 如果将冶金镁砂作为感应电炉的炉衬材料,则由于炉衬厚度的制约,又不宜用湿法打结, 这些不足之处的负面作用就非常明显,因而。氧化镁材料的制成的坩埚容易产生龟裂,间歇 作业的炉子情况尤为严重。
(3)氧化铝质炉衬 氧化铝和锆砂都属于中性耐火材料,其中应用最广泛的是氧化铝,很少采用锆砂作炉衬 材料。 单用氧化铝作炉衬材料,抗裂和防止酸性炉渣侵蚀的能力较强,但不适于造碱性炉渣。 而且,由于其耐火度高、烧结性能较差,炉衬寿命也不很高。
(4)尖晶石型炉衬 尖晶石矿物具有类质同象的特征,品种很多,成分也比较复杂,其分子式可以写成 M2+O·M3+2O3,式中:M2+代表一些二价金属原子,如 Mg、Fe、Zn、Mn 等;M3+代表 一些三价金属原子,如 Mg、Fe、Zn 等。因而,也可写成(Mg,Fe,Zn,Mn)O·(Al,Cr,Fe)2O3 。 尖晶石类矿物所含的二价金属原子中,Mg2+和 Fe2+可以任何比例互相取代;所含的三 价金属原子中,以 Al3+居多,但 Cr3+可以任何比例取代 Al3+,Fe3+则只能在一定的限度内 取代 Al3+或 Cr3+。常见的尖晶石有以下几种: 镁铝尖晶石 MgO·Al2O3 铁铝尖晶石 FeO·Al2O3 铬铁矿(铁铬尖晶石)FeO·Cr2O3 磁铁矿(铁尖晶石)FeO·Fe2O3 镁铁尖晶石 (Mg,Fe)O·(Al,Fe)2O3 锌铝尖晶石 ZnO·Al2O
镁铬尖晶石 MgO·Cr2O3 锌铁尖晶石 ZnO·Fe2O3 锰铬尖晶石 FeO·Cr2O3 锰铝尖晶石 MnO·Al2O3 目前,在各工业国家中,用作炼钢用感应电炉炉衬材料的,主要是镁铝尖晶石(MgO·Al2O3) , 通常简称为‘尖晶石’。纯镁铝尖晶石中,MgO 含量只不过是 28.2%,但仍属于碱性耐火材 料。 镁铝尖晶石系材料的耐火度高,热膨胀系数小,高温下的热稳定性好、抗碱性炉渣侵蚀 的能力强。尤其应该提到的是:MgO 和 Al2O3在烧结形成尖晶石的过程中有 7.9%的体积膨胀, 可以弥补烧结过程中的体积收缩,减少烧结层的孔隙率,这一点与硅砂炉衬的重要优点是一 致的。 镁铝尖晶石基本上没有天然的矿产,都是由人工合成的,制备的方法有电熔和烧结两种 方式。我国冶金行业于 1997 年即参照美国铝业化学公司 MR66 和 AR76 材料的规格,制定了 YB/T 131-1997《烧结镁铝尖晶石》行业标准。 尖晶石型炉衬材料,实际上并不是全部由尖晶石构成,而是以粒状 Al2O3或粒状 MgO 材 料为基础,在其中配加相应的粉状、或细粒状尖晶石形成材料,使之均匀分布在颗粒耐火材 料之间,烧结过程中在氧化铝颗粒之间形成镁铝尖晶石网络,起结合作用。此外,还需要加 入少量硼酸或硼酐,使之能在较低的温度(1300℃左右)即形成尖晶石网络。 美国联合矿产公司、法国米纳克矿业公司、Calderys 公司等知名的耐火材料供应厂商, 都有多种预配的尖晶石炉衬材料供应,可根据企业的炉型和熔炼的钢种选用,但价格都比较 高。 我以为最好的解决方案是:各铸钢企业,根据自己的各项具体条件,通过试验优化、选 定最适宜的配比,自行配制炉衬材料。这样,既可以确保炉衬寿命长、钢的冶金质量高,还 可以较大幅度地降低生产成本。 至于炉衬材料的组成配比,应该根据所用各种原材料的实际成分选取,并经试验确定。 确定炉衬材料配比时,可按以下的目标成分计算: 以氧化铝为基础颗粒材料时 保持炉衬材料中 Al2O3的质量分数为 85~88%左右, MgO 的质量分数为 22%左右; 以氧化镁为基础颗粒材料时 保持炉衬材料中 MgO 的质量分数为 75~85%左右,Al2O3 的质量分数为 15~~22%左右. 3、炉衬材料的粒度级配 坩埚的致密程度对其使用寿命有极为重要的影响,为了使坩埚致密,使孔隙率尽可能地 低,必须重视耐火材料的粒度级配,使大颗粒耐火材料的空隙之间能由细粒材料充填。 为了让大家颗粒状材料打结以后的空隙率有比较具体的印象,这里,以理想球体堆垒的 情况作作简单的说明。 1)紧实度一般的情况 尺寸相同的球体,以正方交错排列方式堆垒的情况如图 1 所示。每一球与相邻的 6 球接 触(周围 4 球,上下各 1 球), 孔隙率为 47.64%。
附件下载:

-
地址:济南市解放路134号 电话:0531-86401781 / 86952422 传真:0531-86465075
邮箱:foundry-shandong@163.com 邮编:250013
版权所有 © 山东省铸造协会 鲁ICP备2021002429号
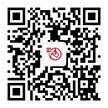
官方公众号