会员登录
MEMBER LOGIN
技术论坛
TECHNOLOGY FORUM
感应电炉熔炼铸钢 炉衬材料与粒度级配
发布时间:
2016-09-26 00:00
来源:
《金属加工(热加工)》
耐火材料炉衬,是坩埚式感应电炉重要组件,影响炉子的熔炼功能、钢的冶金质量,尤其关键的是作业安全。由于坩埚式感应电炉适用于各种铸造合金的熔炼,如铸铁、铸钢、铜合金、铝合金和锌合金等,小型感应电炉,炉衬可购买成型的预制坩埚。实际生产中用于铸钢的坩埚式感应电炉,一般都由铸造厂根据熔炼合金的品种选购适用的耐火材料,自行修筑炉衬,并做好烧结的作业。
1、炉衬用耐火材料的基本情况
常用于坩埚式感应电炉的几种耐火材料,基本成分和耐火性能见表1。
2、适用于炼钢用炉的衬耐火材料
随着感应电炉在铸钢业界应用的发展,自上世纪80年代起,铝镁尖晶石型炉衬材料的应用逐步受到重视,目前,各工业国家铸钢业界所用的坩埚式感应电炉,基本上都采用尖晶石型炉衬。
近年来,我国也有一些铸钢企业采用了尖晶石型炉衬材料,其中,有些厂家是购买国外厂商预配好的材料,虽然使用效果很好,但生产成本提高很多,而且对它的特性不甚了解。在此,我主要是想介绍一些有关尖晶石型耐火炉衬的特性,供业界同仁自行配制炉衬材料、进一步改进炉衬材料时参考。同时,鉴于目前硅砂炉衬、镁砂炉衬、氧化铝质炉衬在我国铸钢业界还都有应用,也顺便对这些材料的特性作一点简单的介绍,供参考。
(1)硅砂炉衬
以硅砂为基本耐火材料修筑的炉衬,通常也称为酸性炉衬。硅砂的优点很多:首先是是资源丰富、价格低廉;而且以硅砂为基本耐火材料制成的坩埚,在接近其熔点的高温下仍具有很好的强度,耐骤冷、骤热的性能好;特别应该提到的是,炉衬烧结过程中,硅砂的石英相变膨胀能弥补烧结过程中的体积收缩,从而提高烧结层的致密度,降低炉衬烧结层中的孔隙率。因此,各国铸造行业中,用于熔炼各种铸铁的坩埚式感应电炉都广泛采用以硅砂为基础的炉衬材料。
但是,SiO2的耐火度低,基本上就不能适应炼钢温度。而且,SiO2在高温下的化学活性很强,能与炼钢过程中的各种碱性氧化物乃至中性氧化物作用,例如,FeO与硅砂接触后易于生成熔点为1205℃的铁橄榄石(Fe2SiO4),铁橄榄石还能进一步与SiO2或FeO作用,生成熔点为1130℃的共晶组分。此外,SiO2还可能被钢液中一些活性较强的元素还原。因此,硅砂炉衬用于炼钢,既不能保证钢的冶金质量,也不能保证炉衬的寿命。从上世纪80年代后期起,各工业国家用感应电炉生产铸钢件的铸造厂,就已经不用硅砂炉衬。据我所知,我国迄今仍有一些企业采用硅砂炉衬熔炼铸钢,这种状况是亟待改进的。
(2)镁砂炉衬
常用的炉衬材料是MgO含量为86%以上的冶金镁砂,是由菱镁矿经高温煅烧制成的。如果将冶金镁砂置电弧炉中重熔,可使其中SiO2、Fe2O3等杂质的含量降低,得到纯度更高(MgO含量在96%以上)的电熔镁砂。电熔镁砂多用于制作真空感应电炉的炉衬。
冶金镁砂的耐火度很高,是碱性电弧炼钢炉的常规炉衬材料,虽然其熔点很高,不容易烧结,而且膨胀系数大,但是由于电弧炉的炉衬很厚,借助于加入大量的粘结材料、用湿法打结,完全可以弥补这方面的不足。
如果将冶金镁砂作为感应电炉的炉衬材料,则由于炉衬厚度的制约,又不宜用湿法打结,这些不足之处的负面作用就非常明显,因而。氧化镁材料的制成的坩埚容易产生龟裂,间歇作业的炉子情况尤为严重。
(3)氧化铝质炉衬
氧化铝和锆砂都属于中性耐火材料,其中应用最广泛的是氧化铝,很少采用锆砂作炉衬材料。
单用氧化铝作炉衬材料,抗裂和防止酸性炉渣侵蚀的能力较强,但不适于造碱性炉渣。而且,由于其耐火度高、烧结性能较差,炉衬寿命也不很高。
(4)尖晶石型炉衬
尖晶石矿物具有类质同象的特征,品种很多,成分也比较复杂,其分子式可以写成
M2+O?M3+2O3,式中:M2+代表一些二价金属原子,如Mg、Fe、Zn、Mn等;M3+代表一些三价金属原子,如Mg、Fe、Zn等。因而,也可写成(Mg,Fe,Zn,Mn)O?(Al,Cr,Fe)2O3。
尖晶石类矿物所含的二价金属原子中,Mg2+和Fe2+可以任何比例互相取代;所含的三价金属原子中,以Al3+居多,但Cr3+可以任何比例取代Al3+,Fe3+则只能在一定的限度内取代Al3+或Cr3+。常见的尖晶石有以下几种:
镁铝尖晶石 MgO?Al2O3 铁铝尖晶石 FeO?Al2O3
铬铁矿(铁铬尖晶石)FeO?Cr2O3 磁铁矿(铁尖晶石)FeO?Fe2O3
镁铁尖晶石 (Mg,Fe)O?(Al,Fe)2O3 锌铝尖晶石ZnO?Al2O3
镁铬尖晶石 MgO?Cr2O3 锌铁尖晶石ZnO?Fe2O3
锰铬尖晶石 FeO?Cr2O3 锰铝尖晶石MnO?Al2O3
目前,在各工业国家中,用作炼钢用感应电炉炉衬材料的,主要是镁铝尖晶石(MgO?Al2O3),通常简称为‘尖晶石’。纯镁铝尖晶石中,MgO含量只不过是28.2%,但仍属于碱性耐火材料。
镁铝尖晶石系材料的耐火度高,热膨胀系数小,高温下的热稳定性好、抗碱性炉渣侵蚀的能力强。尤其应该提到的是:MgO和Al2O3在烧结形成尖晶石的过程中有7.9%的体积膨胀,可以弥补烧结过程中的体积收缩,减少烧结层的孔隙率,这一点与硅砂炉衬的重要优点是一致的。
镁铝尖晶石基本上没有天然的矿产,都是由人工合成的,制备的方法有电熔和烧结两种方式。我国冶金行业于1997年即参照美国铝业化学公司MR66和AR76材料的规格,制定了YB/T 131-1997《烧结镁铝尖晶石》行业标准。
尖晶石型炉衬材料,实际上并不是全部由尖晶石构成,而是以粒状Al2O3或粒状MgO材料为基础,在其中配加相应的粉状、或细粒状尖晶石形成材料,使之均匀分布在颗粒耐火材料之间,烧结过程中在氧化铝颗粒之间形成镁铝尖晶石网络,起结合作用。此外,还需要加入少量硼酸或硼酐,使之能在较低的温度(1300℃左右)即形成尖晶石网络。
美国联合矿产公司、法国米纳克矿业公司、Calderys公司等知名的耐火材料供应厂商,都有多种预配的尖晶石炉衬材料供应,可根据企业的炉型和熔炼的钢种选用,但价格都比较高。
我以为最好的解决方案是:各铸钢企业,根据自己的各项具体条件,通过试验优化、选定最适宜的配比,自行配制炉衬材料。这样,既可以确保炉衬寿命长、钢的冶金质量高,还可以较大幅度地降低生产成本。
至于炉衬材料的组成配比,应该根据所用各种原材料的实际成分选取,并经试验确定。确定炉衬材料配比时,可按以下的目标成分计算:
以氧化铝为基础颗粒材料时 保持炉衬材料中Al2O3的质量分数为85~88%左右, MgO的质量分数为22%左右;
以氧化镁为基础颗粒材料时 保持炉衬材料中MgO的质量分数为75~85%左右,Al2O3的质量分数为15~~22%左右.
3、炉衬材料的粒度级配
坩埚的致密程度对其使用寿命有极为重要的影响,为了使坩埚致密,使孔隙率尽可能地低,必须重视耐火材料的粒度级配,使大颗粒耐火材料的空隙之间能由细粒材料充填。
为了让大家颗粒状材料打结以后的空隙率有比较具体的印象,这里,以理想球体堆垒的情况作作简单的说明。
(1)紧实度一般的情况
尺寸相同的球体,以正方交错排列方式堆垒的情况如图1所示。每一球与相邻的6球接触(周围4球,上下各1球),孔隙率为47.64%。
由图1很容易求得,直径为D的大球的空隙中,可以容纳的小球的最大直径
(2)比较紧实的情况
球体以斜方排列的形式堆垒(图2)时,每一球与相邻的8球接触(周围6球,上下各1球),孔隙率隙率为39.55%。
(3)紧实度最高的情况
紧实度最高的堆垒方式是正方交错排列和和四面体样排列。
均匀的球体以正方交错排列方式堆垒时,每一球与相邻的12球接触,周围4球,上、下各一4球,孔隙率为25.95%。
均匀球体以四面体样排列方式堆垒的情况见图3。每一球与相邻的12球接触,周围6球、上、下各3球,孔隙率为25.95%,
由图3可以计算直径为D的均匀球体的孔隙中可以容纳的小球的最大直径d。
由球体几种堆垒的情况可见,孔隙率只决定于排列方式,与球径的大小无关。球径大,孔隙的尺寸大而数量少。制作炉衬颗粒耐火材料都多角形、甚至是尖角形的,其流动性很差,无论采用何种打结方式,舂得最紧实的,其孔隙度也不会低于30%。
为了降低炉衬的孔隙率,简便易行的措施是使炉衬材料中颗粒尺寸不那么均匀,而且细粒材料可以进入紧密排列的粗颗粒之间,最低的要求当然是必须有d<0.414D的细粒。粒度级配的要求就是由此而来的。
当然,耐火材料的颗粒状况比理想球体复杂得多,粒度分布的情况也极不规律,不可能简单地靠计算求得最佳的粒度级配方案。最好的办法是:各铸造厂都就自己原材料的实际状况,通过试验,求得最合适的级配方案。
试验的方法很简单:将不同粒度的材料按一定的配比混匀,在一定的压力作用下使之紧实成形,然后测定其体积密度。原材料供应条件改变时,也要经试验考核粒度级配方案。
德国、日本和美国相关行业推荐用于硅砂坩埚的粒度级配见表2。
由于粒度级配的目的是使颗粒的堆垒致密,与材料的性质无关,所以这一原则可适用于各种耐火材料。德国还就不同容量坩埚的材料推荐了不同的粒度级配。
4、炉衬材料的烧结
坩埚式炉衬都是将颗粒状耐火材料打结、舂实,再经烧结制成的。“烧结”是确保炉衬致密而具有相当强度的重要措施。
“烧结”是在高温下使粒/粉状集合体中颗粒的接触面上出现液相、逐渐形成连续的网络,进而将颗粒连接成一个整体,并借助于扩散、传质等机制使孔隙率降低到最小程度,最终成为坚实致密烧结体的过程。
“烧结”是一项比较古老的工艺,对其进行较深入的研究则是近几十年的事。但是,目前的认识,仍然不过是由烧结过程的宏观观察、并用简化的模式考核所建立的。随着感应电炉应用的不断扩展,在这方面,研究、改进的空间非常广阔。
由于受到多方面的制约,坩埚式感应电炉的炉衬厚度薄是其重要的特点,但是,经打结、烧结后的炉衬却不能烧结成为一个整体,因为,整体烧结的炉衬中,如果某处因不可控制的因素存在薄弱环节,并在反复的热应力作用下产生裂纹,裂纹就易于扩展到整体,从而使金属液渗透到感应线圈,导致重大事故。
炉衬烧结后,其断面应该是3层结构:形成炉膛、与钢液接触的一层是烧结层,厚度约占炉衬厚度的35~40%,其特点是烧结网络致密、孔隙率低、强度高;与烧结层相接的是半烧结层,厚度大体上与烧结层相同,其特点是烧结网络不完全,强度不高,因而可以缓冲烧结层所受的热应力,如果烧结层产生裂纹,可阻止裂纹向外延伸;炉衬的外缘、在感应线圈与半烧结层之间的是未烧结层,耐火材料仍保持打结后的颗粒状态。这一层,有隔热的作用,并能减缓烧结层向线圈的热传导,其厚度约占炉衬厚度的25~30%。
尖晶石型炉衬的烧结过程,大致可分为3个阶段:
第一阶段:加热温度在850℃以下,主要作用是使炉衬材料比较彻底地脱水;
第二阶段: 加热到850~1400℃,主要作用是形成尖晶石网络;
第三阶段:加热到1300~1700℃,尖晶石网络长大,在表面张力的推动下增强扩散、传质的功能,孔隙率显著降低,烧结层趋于紧密。
附件下载:

-
地址:济南市解放路134号 电话:0531-86401781 / 86952422 传真:0531-86465075
邮箱:foundry-shandong@163.com 邮编:250013
版权所有 © 山东省铸造协会 鲁ICP备2021002429号
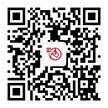
官方公众号