会员登录
MEMBER LOGIN
技术论坛
TECHNOLOGY FORUM
美国先进的无旋式曲轴感应淬火和回火技术
发布时间:
2014-11-19 00:00
来源:
介绍一种曲轴感应热处理的新工艺,该工艺不同于常规的工艺,曲轴不旋转。与传统的感应淬火设备的操作相比较,本文概述了该项新静态方法的技术优点, 即节约成本和空间。
曲轴广泛应用于内燃机、泵、压缩机等,并且属于最关键的那一类部件,特别是对于质量在15~40kg之间的发动机。同时,对于有些曲轴的质量超过700kg的曲轴(用于造船工业或火力发电的固定发动机的曲轴)而言同样如此。
一个发动机曲轴, 特别是铸造件或锻造件,包括由曲臂/平衡块相互连接的一系列曲柄销和主轴颈。钢质锻件、球墨铸铁件、微合金锻件和奥贝球墨铸铁件都是最常用的曲轴材料。曲轴最重要的一些要求是:高强度和高弹性、良好的抗疲劳和抗磨损性能、刚度好、重量轻、低噪音和扭转振动小(NVH 特性)、几何精度高、长度短、低速扭转时高承载能力和低成本。在曲轴制造质量中,热处理起了很重要的作用。
曲轴旋转的常规技术
现有的大多数曲轴感应淬火设备都要求曲轴在加热过程中旋转。当曲轴绕主轴线旋转时每个曲柄销和主轴颈通过一个靠近该曲柄销和主轴颈表面的U型感应器来进行加热。因为曲柄销轴线在主轴线半径方向,所以曲柄销将环绕主轴线运行。曲轴的旋转速度一般在24~32r/min之间变化。因此,U 型感应器以及感应淬火设备的一些其他相当笨重的部件(包括供电输出变
压器、水冷线圈、汇流线圈、电缆等等),其重量通常超过900kg,必须与连杆轴颈的轨道一起移动。该重型系统的圆形轨道运动必须保持非常精确。所有这些因素导致了常规感应淬火设备的设计相当复杂、敏感、笨重、噪音大并且费用高昂。
设备的可维护性、可靠性和硬化模式的可重复性也是常规技术用户所关心的问题。特别是线圈的使用寿命短一直是个难题。而通常“U”形线圈的使用寿命不到2~ 3个星期。在使用现有的旋转式曲轴淬火技术时,导致线圈的使用寿命短有几个因素:
(1)常规技术要求线圈和热处理工件的表面之间的空隙非常小(有时小于0.5mm)。狭小的空隙,相对较长的加热时间(7~12s),曲轴表面的温度(950℃以上)以及潮湿的工作环境都为铜质线圈件的应力腐蚀提供了有利的条件。
(2)铜焊线圈复杂的几何形状具有众多接头,再加上大量的热量以及电磁力的存在为应力疲劳、线圈失效和裂缝扩展提供了有利的条件,特别是在感应线圈热量聚集的铜焊接头部位。
(3)由于狭小的空隙,线圈经常与旋转曲轴的表面发生意外碰撞(线圈“坐”在曲轴轴颈上),因而线圈的损坏(线圈的过度使用)经常造成线圈的过早失效。这种现象的发生是由于硬质合金导向器(定位器)的磨损无法控制,或在其他方面,如无接触线圈位置跟踪系统出错。
新颖的曲轴静态淬火工艺
为了避免以上所述的缺点并且解决用户所关心的曲轴旋转的常规淬火工艺的其它问题,美国密安州Madison Height市的Inductoheat公司提出了一种新型无旋式技术。
该曲轴静态淬火工艺无需在加热和淬火周期内旋转或移动感应器或曲轴,同时,在使用环状夹紧型线圈时无需大电流接触。第一台机器已制造出并用于一家世界领先的汽车制造厂家,并且第二台也接近完工阶段。
无旋式硬化系统的优点立刻被用户的材料专家、制造工程师和质量专家所认可。系统其中的一些特性描述如下。
无需曲轴旋转的静态加热方法具有几个实际的益处,诸如操作简单、可靠性高、可维护性、紧凑性(仅占常规工艺要求的占地面积的20%)以及成本降低。根据用户的要求,曲轴可垂直或水平地进行操作和热处理。
外形尺寸变形的减小历来就是曲轴热处理中最关键的因素之一,因为它直接影响到磨削去除的金属量。影响曲轴变形有几个因素包括有材料性能、硬度分布、残余应力等。其中最重要的一个因素就是在曲轴内部(包括主轴颈、曲柄销和平衡块)产生的总热量。被加热金属的量越大,金属膨胀越大,从而导致变形越大。
曲轴静态淬火工艺技术显著的优点之一就是加热时间短,一般在1.5~4s之间(相比较常规工艺的7~12s)。由于加热时间短,仅有很少量的金属被加热。其热影响区的极小化导致金属膨胀的最小化,从而显著减小了尺寸和外形的变化(一般变形小于0.025mm),因而磨削的要求也就得以降低。
由于加热时间短,减少了曲柄销和主轴颈表面的晶粒生长、脱碳和氧化,提高了硬化区的冶金性能。该硬化区已明确定义,并且“边界清晰”,不会因加热时间较长而出现“模糊过渡区”。该区由带有极少量残余奥氏体的细晶粒马氏体微观组织构成,无任何自由铁素体在常规工艺中,当用户研究硬度分布时经常会观察到临界数量的自由铁素体。它在曲柄销和主轴颈表面上的存在对曲柄销和主轴颈的耐磨性和其他一些重要特性造成危害。
加热时间短也能产生通常所称的“感应超高速硬化”现象,此时硬度比给定钢号的正常最大硬度提高2~4HRC。这就允许用户使用更低的钢号(更低的碳含量)而不会失去预期的表面硬度以及产品的硬度分布。
考虑电磁方面,曲轴的任何加热部位(主轴颈、曲柄销、油封)将曲轴静态淬火工艺感应器视为环状封闭型线圈,感应涡流沿着热处理部位(有一普通涡流环)的周围流动。另一方面,当使用常规的U形感应线圈设计方法时,热源局限于局部的涡流本身,从而导致线圈功效的降低,特别是在居里温度之上时。因此曲轴静态硬化工艺线圈的电效率高于U形线圈。另外,同常规技术相比,曲轴静态硬化工艺线圈对工件和线圈之间的空隙变化的敏感性会大大降低,并允许在线圈和轴颈表面之间有更大的空隙。
曲轴的加热部位(主轴颈、曲柄销、油封)将曲轴静态淬火工艺感应器视为传统的环状圆柱形线圈。因而,产生对称加热并且硬度分布更加均匀。相反,当使用U 形线圈时,无对称加热模式, 并且在任何给定时间里,仅加热曲轴部位(即:主轴颈或曲柄销)的一半。曲柄销和主轴颈的另一半采用“浸湿冷却”模式。U形感应器的无对称加热性能会导致硬度分布不均匀并且还可能造成该加热工件的椭圆变形。
既然采用曲轴静态淬火工艺的加热时间只是常规工艺的三到四分之一,当使用新技术时,线圈的热效率也将增强(辐射和对流损失减少)。曲轴静态淬火工艺技术对于曲柄销和主轴颈的相邻物体(曲臂和平衡块)的不规则外形不是很敏感。线圈设计结合了大量的新型电磁解决方案,从而使得该技术实际上对相邻物体的差异不再敏感。
静态曲轴硬化工艺的控制能力相当出色。除了可以改变热处理轴颈宽度方向的硬度分布外,还可以改变曲柄销和主轴颈周围的硬度分布。这种良好的控制能力也可用来防止局部的加热不足或者过热。例如:油孔区域通常被认为是“麻烦区”。油孔以表面为基准经常转变角度(油孔),因而一边的金属质量相对于另一边减少了。由于质量的减少,在该区域应存在金属过热的危险,结果就有可能产生裂纹甚至出现局部熔化。曲轴静态淬火工艺采用先进的线圈设计概念显著地降低了该区域的感应功率密度并且解决了以上问题。另外,当轴颈左右两边的平衡块不一致时,可控制加热以防止加热模式从一边转到另一边时发生改变。这种控制“轴颈径向方向”加热方式的能力也可应用于无对称孔区域。
“从上至下”和“从左到右”横截面也可控制。这包括所谓的“鱼尾”形区域(或线圈的“分裂”区)。在传统的感应系统中,由于电流抵消现象产生了电磁场的变形。作为这种“鱼尾”效应的结果,可能出现软点或硬化模式的“ 颈缩”。实际上,这就是在曲轴静态淬火工艺技术发展阶段有待解决的主要问题之一。在静态淬火工艺中无明显软点或硬化模式的“ 颈缩”。此外,当使用静态淬火工艺时,无“双环”模式出现。事实上,一些使用硬质合金导向器(定位器)的U 形感应器有着明显的缺点:
(1)定位器的适当调整要求特殊的组织培训及丰富的经验并且还存在人为误差。
(2)在高温时,曲柄销/ 主轴颈表面上的硬质合金导向器将“外来夹杂”带入轴颈表面,有时它可增加应力。不过,这个特殊因素如果使用严格的最终磨削方法则可以消除。
(3)必须精确地监控硬质合金的磨损及其位置,这通常是相当艰难的任务。否则,硬化模式就可能转换或者感应线圈摩擦曲轴表面,从而降低线圈的使用寿命。
(4)每个定位器都不过是又一个可能出错的零件,因而机器的可靠性无法保证。
为了提高线圈的电效率, 常规曲轴淬火技术必须将叠片结构放置在接近于加热表面的位置(被加热表面和叠片结构表面的空隙通常小于0.5mm)。热曲轴表面的辐射和对流热量的散逸以及内在热量的循环(较曲轴静态淬火工艺的热量循环时间要长3~4倍)也缩短了这些叠片结构的使用寿命并且导致它们的过早老化。“加热-冷却”循环、电磁末端效应和实际的电磁力也降低了叠片结构的使用寿命。
有了先进的静态线圈,不再需要这些叠片结构。静态线圈采用的是特殊的更耐用的导磁体,更难达到磁饱和,并且不会产生像常规方法使用的叠片结构那么多的热量或电磁力。
由于感应器的电磁“闭形”,线圈功率因素非常重要,而线圈区的漏磁量(线圈外部磁场)可以忽略不计。
由于加热时间短,曲轴的残余热量减小,这是曲轴静态淬火工艺技术的另一个显著的优点。在许多情况下,残余热量少带来的优点是免去了特殊的冷却系统,因而能节约大量的资金以及地面空间。图5、6、7用图解方式比较了曲轴静态淬火工艺与使用U 形感应器的常规技术的“时间—温度”分布情况。比较的结果通过使用专业版感应加热软件“ADVANCE”获得。为便于比较,假设采用常规方法和曲轴静态淬火工艺技术时,淬火之前的表面温度相同。该新技术同时也是节约空间的技术。与常规工艺相比较,显示了曲轴静态淬火工艺感应淬火/回火系统的紧凑性。无需曲轴旋转的静态加热方法在人机工程学上很具有吸引力并且存在另外一些优点,该优点影响到了曲轴感应淬火/回火工艺的其他方面。
附件下载:

-
地址:济南市解放路134号 电话:0531-86401781 / 86952422 传真:0531-86465075
邮箱:foundry-shandong@163.com 邮编:250013
版权所有 © 山东省铸造协会 鲁ICP备2021002429号
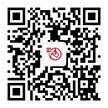
官方公众号