会员登录
MEMBER LOGIN
技术论坛
TECHNOLOGY FORUM
【成功案例】重型卡车平衡轴支座结构优化
发布时间:
2022-03-29 20:06
来源:
前 言
本案例针对平衡轴支座在道路试验过程中发生断裂的问题,通过理化分析和铸件解剖,查找出断裂原因为铸造缺陷引起,并对平衡轴支座结构和铸造工艺进行优化设计。采用有限元方法和AnyCasting数值模拟方法分析了该零件在整车不同工况下的应力大小及应力分布情况及铸造工艺的可行性。结果表明,平衡轴支座结构优化后可满足整车强度需求,铸造工艺改进后消除了铸造缺陷。经实车试验,验证了平衡轴支座的可靠性,并对铸件设计流程进行了总结和规范。
1 平衡轴支座结构优化
1.1 平衡轴支座断裂原因分析
某重卡自卸车完成整车及零部件设计后,为了验证整车满载情况下各零部件的使用性能,对此辆样车安排10000 km道路试验。但是,道路试验进行到1000 km时,即出现平衡轴支座断裂现象。断裂发生在平衡轴支座圆轴根部,断裂处局部及断口形貌见图1。断裂处附近锥度表面环向约1/2区域有磨损,漆膜被完全磨掉,露出零件金属色,其余部位漆膜基本完整。断口较不平整,被泥浆覆盖,简单清洗后可见断口上有明显的铸造缺陷,缺陷面积约占整个断面的50%。
在失效零件断裂处附件进行微观检查,该区域石墨球化及大小均无异常,基体组织呈明显的枝晶分布,基体为中等片状珠光体+铁素体+少量碳化物,珠光体有偏聚现象,检查面上可见微观疏松。石墨形态、微观疏松及基体组织见图2。经检测平衡轴支座断裂处附近基体硬度平均为HBW 211(公司内标准要求160~230),符合标准要求。为了进一步确认平衡轴支座内部确实存在铸造缺陷,对该铸件按照原铸造工艺重新进行生产,铸件毛坯经简单清理后,将平衡轴支座从轴的中间部位锯成两半,解剖后的结果看到平衡轴支座轴根部确实存在缩孔铸造缺陷,且缩孔位置与断裂件缺陷位置基本一致(图3)。平衡轴支座断裂失效的主要原因为:失效零件断裂处存在严重的铸造缺陷,使其局部承载能力显著下降,导致整车试验过程中引发断裂事故。
1.2 平衡轴支座结构优化
结合铸造工艺及存在的缺陷问题,对平衡轴支座原结构进行详细分析,发现在轴根部位置壁厚较厚,导致轴根部形成较大的热节,且中间位置布置的圆环形加强筋也在轴根部,不利于此处砂芯的排气,因此造成铸造过程中易产生缩孔缺陷。结构优化主要以减轻壁厚、调整腔体结构为平板布置加强筋、优化圆轴根部圆环形加强筋的布置为主,以此来缩小圆轴根部的铸造热节,从而避免铸造缩孔倾向。
1.3 改进后平衡轴支座结构静力学分析
在Hypermesh中建立平衡轴支座与车架的有限元模型,设定平衡轴支座原材料为球墨铸铁QT500-7,弹性模量2.1×105 MPa,密度为7.8 g/mm3,泊松比为0.28。重型卡车在实际使用过程中板簧和车架对平衡轴支座施加的外载荷较大且种类很多,在设计过程中主要考虑四种工况,分别是垂直加速度、转弯、车架扭转和制动,分析平衡轴支座在各种工作环境中整体的刚度、强度和安全系数性能,为设计提供理论指导。
1.4 平衡轴支座改进方案铸造工艺分析
利用AnyCasting软件对平衡轴支座铸造时金属液充型和凝固过程进行数值模拟分析,以此分析结果初步确认平衡轴支座改进方案是否可避免铸造缺陷,并为铸造工艺设计提供参考。平衡轴支座采用的是湿型砂铸造工艺,前期试制阶段制作木模1套(包括芯盒3套),改进后的平衡轴支座铸造工艺与原方案基本一致。考虑原方案铸造存在缺陷风险,此次在铸造工艺中增加设置2处外冷铁及补缩冒口,铸造工艺简图如图7所示。
根据上述铸造工艺设计,在AnyCasting软件重建立平衡轴支座分析模型,设定分析条件并进行数值模拟分析,结果显示,铸件最终凝固位置位于冒口中,从数值模拟分析角度确认圆轴根部的铸造缺陷已得到解决。
其次,对该铸件重新制作模具,进行铸件试生产后,对铸件进行实物解剖,解剖后可以看到,铸件内部组织致密,没有发现铸造缺陷,此结果与AnyCasting铸造工艺数值模拟分析结果一致(图8)。
平衡轴支座改进前后方案,各工况下安全因子结果见表4。平衡轴支座改进方案结构静力学分析最小安全因子均>1,工况计算合格;各工况下最大应力比原方案均有降低,安全性能得到了极大提高。结构优化和工艺改进,铸造工艺性优于原方案,重量比原方案减轻10%,铸件制造成本降低10%。
1.5 铸件类产品设计规范
为了规范铸件类产品设计统一,加快铸造和机加工单位的生产节奏,节省生产成本,根据设计人员的设计经验,总结本次平衡轴支座改进优化过程,并在公司内部发布《铸件类产品设计规范》,为公司内铸件类产品设计过程提供参考。铸件设计流程见图9。
2 结束语
通过对平衡轴支座断裂失效原因进行深入研究和分析,准确地查找到导致平衡轴支座断裂的原因为铸造缺陷引起。根据铸件缺陷原因确定结构改进优化方案,改进后的方案经铸件静力学分析、铸造工艺数值模拟分析及实物验证,消除了铸造缺陷,并在后续的30000 km试验中未出现失效现象,保证了整车的使用性能和可靠性。平衡轴支座改进方案安全性能得到了极大提高。结合平衡轴支座设计改进过程,在公司内部发布《铸件类产品设计规范》,在铸件设计流程中引入铸件静力学分析和铸造工艺数值模拟分析过程,统一规范铸件设计过程,提高新产品铸件设计开发质量和正确性,从而缩短新产品研发周期。
作者简介:
李运成(1979-),男,工程师,主要从事汽车铸件结构设计、优化、分析及铸造工艺的研究,陕西重型汽车有限公司
本文节选自《铸造》Vol.68 No.11 2019《重型卡车平衡轴支座结构优化》
附件下载:

-
地址:济南市解放路134号 电话:0531-86401781 / 86952422 传真:0531-86465075
邮箱:foundry-shandong@163.com 邮编:250013
版权所有 © 山东省铸造协会 鲁ICP备2021002429号
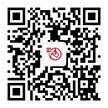
官方公众号