会员登录
MEMBER LOGIN
技术论坛
TECHNOLOGY FORUM
进一步发挥感应炉熔炼优势提升铁液质量
发布时间:
2013-09-04 00:00
来源:
钱 立
(河北工业大学,天津300021)
多年来,采用感应炉已经成为铸造企业技术改造、产品升级的主要措施之一。不仅众多中小企业(尤其是多牌号生产)青睐感应炉,就是生产风电铸件的大型工厂亦改为多台中频炉协同作业的方法。最近,玉柴集团打造世界最大的柴油机铸件生产基地,其铸造中心采用了单一感应炉熔炼,在保证质量的基础上,降低了炉料成本,减少了生产工艺和生产人员。
1 感应炉熔炼采用无芯中频炉
感应炉有有芯和无芯之分。感应炉熔炼应采用无芯炉。无芯炉变更铁液品种方便,可以冷炉料起动,提温迅速,生产率高,电磁搅拌作用好,筑炉修炉方便。频率采用中频范围。与工频炉相比,无需开炉块;功率密度大,起动和熔化快,节约电耗;功率可无级调节,且可在不同炉体间任意分配;可自动变频以适应炉料参数的变化;搅拌力度和“驼峰”可控;对炉料块度并无苛求,从块料到切屑均可。一般频率随炉子容量的增大而减小,例如0.1~60 t 炉子,频率在2500~150 Hz。近年来,IGBT 半桥串联逆变中频电源因其负载适应范围宽,熔炼过程中可保持恒功率运行,电源功率可以共享等高性能特点,在中型和小型炉子上得到了广泛应用。
熔炼灰铸铁和球墨铸铁时,采用酸性炉衬,炉衬材料来源广、价格较为便宜。天然石英砂最高工作温度为1 650℃,熔融石英砂则为1 660℃。
工频有芯炉适宜作保温炉或浇注炉使用。某厂冲天炉铁液连续流入立式有芯炉,有芯炉根据造型浇注线的需要随时出铁。因此对于频繁出铁和平衡铁液供求关系十分有利。国外某厂是一个大冲天炉分别供应了3 个有芯保温(储存)炉,再由铲车转运铁液至气压浇注炉进行浇注。有芯保温炉炉膛密封性好、元素烧失极少。作浇注炉使用时能准确控制浇注温度和浇注量。
本文以下提到的感应炉均指无芯中频感应炉。
2 感应炉熔炼的优势
感应炉熔炼具有以下优势[1]:
(1)感应炉热量产生于炉料内部,无需外界传导,因而热效率高,加热速度快。
(2)铁液过热度容易调节,出铁温度高。
(3)元素烧损少,铁液中气体含量和非金属夹杂物少。没有冲天炉铁液的焦炭硫污染问题。
(4)由于电磁搅拌作用,铁液的化学成分和温度均匀。
(5)熔炼工艺稳定、易控,铁液化学成分准确。
(6)可以多用或全部使用废钢,用增碳的方法生产合成铸铁。
(7)切屑和边角碎料等细小的难以在冲天炉内直接利用的廉价废料,在感应炉内借助电磁搅拌作用,很容易卷入铁液而迅速熔化,而氧化损耗却较少。若装料期加入,因切屑粒度小,感应电流分布于整个切屑的断面,熔解较快,但烧失较多。
(8)感应炉的烟气和粉尘较少,噪音小,作业强度低,环保治理比较方便。
(9)生产安排灵活,开炉、停炉方便。
(10)容易实现自动化管理。
然而,感应炉熔炼亦存在一些不足和问题。如不能了解其冶金特点,采取相应的操作对策去扬长避短是难以获得优质铁液的。此时,非但不能得到所需的金相组织,还会恶化切削加工性能,产生某些收缩缺陷等。
3 感应炉熔炼的冶金特点
感应炉的冶金特点与冲天炉不同。
(1)没有氧化性的燃烧炉气,又是采取批料间歇熔炼,因而元素损失少,化学成分准确、稳定。
(2)电磁搅拌作用在一定程度上有利于非金属夹杂物的合并、上浮,并增加了与熔渣接触机率而为熔渣所收容。同时亦有利于铁液中溶解的H、N、O 的排除。
(3)熔渣不能感应发热,渣温低。加之坩埚的高径比大,又没有冲天炉内铁滴与渣滴交互接触的机会。因此,熔渣内物理化学过程不活跃,熔渣的冶金功能极为有限。熔渣主要起覆盖保护和一定程度的收容夹杂物的作用。
(4)感应炉熔炼后期,随着铁液温度的升高,当达到所谓平衡温度以上时,发生以下反应:
SiO2(炉衬)+2[C]→[Si]+ 2CO↑
( SiO2)(液中)+2[C]→[Si]+2CO↑
此时,对FeO、MnO 有类似的反应。感应炉内C 的还原作用是冲天炉无法比拟的。发生上列反应的条件一是高温,二是缺氧和没有氧化性气氛。冲天炉炉缸里只有在湿底(炉缸不过空气)时,才能满足Si、Mn、Fe 从氧化物中被C 还原的条件。冲天炉的炉缸较浅,铁液流经炉缸的时间比较短暂,反应没有感应炉内从容、充分。C 作为还原剂,产生的CO 造成熔池“自沸腾”,对铁液起到了脱气除杂的净化作用。
(5)铁液的过冷倾向大。图1[2]表明,在相同CE 下,感应炉铁液的共晶过冷度比冲天炉铁液大。这是由于:①高温下,铁液中由生铁和回炉料带来的石墨的减少和消溶;②熔炼后期,铁液中SiO2 因与C 反应,而使可作为外来晶核的SiO2 减少,乃至丧失;③感应炉铁液的[S]、[O]明显低于冲天炉,一般[S]<0.05%,[O]<0.001 5%。如此低的O、S 含量,对于灰铸铁来说,是难以指望硫氧化物的外来晶核作用了。
铁液过冷倾向大,将导致以下情况出现:灰铸铁中出现过冷石墨,甚至产生自由渗碳体;将使球墨铸铁出现麻口组织、并减少石墨球数量;产生自由渗碳体的结果,使铸铁缩松缩孔倾向增大;使薄壁灰铸铁件出现渗漏;使切削加工性能恶化,降低机加工工效,增加刀具损耗,提高加工费用,这是用数控机床或加工中心大批量生产企业所十分忌讳的。
4 感应炉优质熔炼的控制要点
4.1 把化学成分控制工作做细
虽然与冲天炉相比,感应炉有元素烧失少,化学成分准确、稳定的先天优势,但如果后天失调,这个先天优势是会打折扣的。准确控制化学成分还需有四个前提。
(1)用净料 炉料杂乱、不干净、锈蚀多,则元素烧失增大,也无法使烧失稳定。此外,感应炉炉渣的冶金功能差,也要求炉料纯净,严防P、S、O 和微量元素含量不明。
(2)准确配料 根据元素的烧失规律,正确进行配料。特别不要忘记把熔炼后期的脱C 量考虑在配C 量之内。配料不准确,会延长熔炼时间,增加能耗。
(3)配备多功能热分析仪和直读光谱仪 及时掌握化学成分和凝固等信息,进行炉内或炉前调剂。当感应炉与冲天炉或高炉双联时,适时而准确的测报更为重要。
(4)把握火候,控制好终点 关于终点温度和时间的控制,后叙。
4.2 合理加料
七手八脚、胡乱加料、野蛮加料的现象,在一些工厂常有发生。有些“规程”只侧重于操作性的表述,如①炉底垫轻薄料;②料块要合理,切忌厚大(电频率在100~500 Hz 时,最佳平均料径为230~100 mm);③装料要紧密,但不能在熔化期发生棚料,等等。这些规定,对于保护炉底免受撞击和过热,炉料顺行和热利用,无疑是必要的。然而,从冶金学视角考虑,强调以下几点更为重要。
(1)炉料装入顺序,应保证炉底尽早形成高碳熔池。令熔点低的回炉料先装,再装生铁,熔点高的废钢装在其上。这样,供电后炉底很快便形成熔池,废钢浸入其中,表面因增C 而降低熔点,起到了助熔作用。还必须指出,废钢比生铁易于氧化,当温度高于700℃以后,废钢表面氧化加速。若废钢能尽快熔于铁液,无疑对于减少氧化也是有益的。
化学成分对于熔点的影响是基于Fe-C 相图中液相线的变化:随着C 含量的提高,钢的熔点降低。同样的道理,一些高熔点铁合金,可以利用表面增Fe,降低液相线温度,来达到助熔的目的。笔者在熔炼有Mo、W、B、V 等的铸铁时,较早地将FeMo、FeW、FeB、FeV投入熔池,起到了助熔作用。借助电磁搅拌作用,铁液成分很快就均匀了。
(2)熔炼初期切忌底部熔池过热,以免炉底因发生SiO2(炉衬)+2C=Si+2CO 反应而致的化学侵蚀。铁液的过热还会加剧元素的烧损和含气量的增加。
(3)随着炉料的逐步熔解,应适时适度续料,前一批料尚未化尽前,投入后续料。投向熔池的炉料要干燥、无锈蚀,以防铁液氧化和气体含量增加。在冬季,往熔池加冷废钢,会“炸溅”,产生安全事故。切屑宜加入熔池。装料期加,会加大元素烧损。
(4)装料初期应随着加金属料,加入适当的造渣剂(清渣剂),使炉底的熔池早早处于熔渣的保护之下。以后,在熔化期视需要,再补充渣料;炉料熔清后,可扒渣,再造渣。总之,熔炼过程中,提前造渣,造好渣,补渣换渣,是不可忽视的环节。
4.3 精益净化
研究表明,仅仅关注铸铁的基本化学成分和组织是不够的。铸铁性能的发挥和铸件的失效,往往与铸件中的铸造缺陷、组织缺陷、某些同溶元素和晶界脆性相的存在密不可分。而所有这些,多数与铸铁中的非金属夹杂物及气体有关。因此,必须发挥感应炉内的精益净化作用。
电磁搅拌有助于金属料和增碳剂的加速熔解吸收,使化学成分和温度均匀化,也有利于脱气和去除非金属夹杂物。但脱气和去杂的作用是有限的。感应炉多采用单相供电,产生如图2 所示的两段四区电磁搅拌。由图可知,下部两区对于夹杂物的上浮有一定的抵消作用,也削弱了电磁搅拌的脱气作用。
平衡温度是决定反应SiO2+2C=Si+2CO 方向的温度。当温度大于平衡温度时,反应向右进行,反之则反应向左进行。单质状态下,平衡温度为1 645.8℃。铁液中的C 含量和Si 含量影响平衡温度:随着C 含量的增加或Si 含量的减少,平衡温度降低。在通常灰铸铁或球墨铸铁铁液成分下,平衡温度约在1 425~1 400℃,对于低温用铁素体球墨铸铁则约在1380℃左右。当熔池温度高于平衡温度时,反应产物CO 造成熔池沸腾。生产中为了保证足够的沸腾力度,一般取平衡温度以上50℃,称作沸腾温度。CO 造成的沸腾是发生于整个熔池的,CO 是往上逃逸的。因此,其净化作用是电磁搅拌无法比拟的。利用熔炼后期熔池的“自沸腾”净化是感应炉熔炼的一大特色。通过“自沸腾”能很好地降低铁液中H、N、O 的溶解量,并在气泡上浮过程中,携带非金属夹杂物进入熔渣。
吹Ar 净化是一种有效的辅助手段。通常可采用炉内或包内插管吹Ar 或炉底透气砖吹Ar,亦有在炉底安置气体扩散器,再在其上捣搐特定的耐火材料层,令Ar 通过这一可透气的烧结层达到净化目的。
研究表明,除N 是除气的重点。降低铁液中的N,不仅可以免除N 气孔,更主要的是提高球墨铸铁,乃至提高抗磨白口铸铁的韧性。
除了以上的方法可以除N 外,还有吹O2 或吹CO2 除N 和脱N 剂脱N 等的试验与实践。
4.4 防止后期H、N、O 回升即便进行了净化处理,如果此后操作不当,H、N、O 仍有回升的可能。为此,须特别注意几点。
(1)后期不能投潮湿的物料。
(2)选用O、N 低的增C 剂。
(3)电磁搅拌力与输入功率成正比,与频率的平方根成反比。加入增C 剂后,一般可用调低频率的方法,促使增C 剂的溶吸。但搅拌力度(尤其是在无熔渣覆盖的情况下)不能过度。否则,“驼峰“高,氧化吸气风险大。
(4)“自沸腾”或吹Ar 等处理不能过于激烈。
(5)铁液化学成分和温度合格后,停电扒完渣,要尽快倾炉出铁。出铁最好一次完成。分包出铁或遇意外情况,要对剩余铁液供电保温,无渣保护的铁液,氧化烧失和吸气问题会突出起来。
4.5 正确控制终点
炉料熔清后,熔池升温加快,经过平衡温度、沸腾温度、临界温度,而达到过热温度。所谓临界温度是指当超过这一温度时铁液中石墨核心数明显减少,铁液白口倾向增大,铸件或试样中石墨形态发生变异,产生过冷石墨甚至出现自由渗碳体。不同资料所提供的临界温度数据不甚一致,一般为1 455~1 510℃。临界温度与炉料状况及铁液化学成分有关,如生铁牌号高则临界温度高;废钢配比多,生铁用量少则临界温度低;铁液C、Si 含量低则临界温度低等。此外,使用什么样的增C 剂也影响到临界温度。熔炼最终的过热温度视铸铁材质、铸件体量大小,以及炉料等情况的不同而定,一般为1490~1 550℃。
经过1 490~1 550℃过热的铁液,淡化了炉料的不良遗传性影响,也加大了过冷倾向。但只要作好预处理和孕育处理,孕育效果会发挥得更好,有利于石墨和基体的细化。必须强调,过热温度切忌随意提高。必须指出,在过热温度下停留时间不能长。否则会产生“死铁液”(这种情况常在夜班保温,第二天早班使用的铁液中发生)和H、N、O 回升的现象。
4.6 预处理
感应炉铁液的自发形核能力差,白口倾向大,必须认真做好孕育处理。与相同化学成分的冲天炉铁液相比,感应炉铁液的孕育量要多出0.1%~0.2%。对于高质量的铸件,出铁前还应该在炉内进行预处理。晶型石墨和SiC 的形核能力强,是应用最普遍的预处理剂,其次是孕育级的硅铁。
此外,还可在包内进行预处理。炉外预处理技术可查有关报道。对灰铸铁而言,感应炉铁液的S 含量低,不利于孕育形核。需将提高至0.07%~0.10%。因此,从广义的预处理概念上讲,铁液增S 也是一种预处理。FeS 的熔点为1 193℃,它能全部溶于铁液。S 的回收率视加入时机和加入状况而定,熔炼后期镜面加入时回收率可高于90%,装料期加入则回收率降低。为了降低费用,有的工厂使用黄铁矿增S。
4.7 节能快熔
“十二五”期间,单位 GDP 能耗要降低16%。节能减排已被列入地方政府官员的业绩考核之中。熔炼工部节能是企业节能的重中之重。感应炉节能快熔可采取以下措施网。
(1)提高比功率,以实现高的电效率和高的热效率并实现快速熔炼。目前0.5~60 t 炉子的比功率设计为1 000~600 kW/t。
(2)一拖二,即一套电源同时向两个炉体供电,功率在两个炉体间任意分配。整个熔炼过程以恒功率运行,功率利用系数几乎可达100%。
(3)尽量安排在较大容量的炉子上熔炼。据测算,5t 炉比2t 炉的吨铁电耗可减少3%~4%。
(4)作业制度上,采取连续熔炼。
(5)增设炉盖,并减少开盖率。带盖作业与敞口作业相比,液面热损耗功率可降低50%~60%。
(6)使用净料,禁止锈蚀料和含坭带砂料入炉。
(7)掌握炉料成分,准确配料,免除成分超标而导致的不必要的调整工作。
(8)设法缩短装料、熔化、取样和检测时间,提高功率利用率。
(9)避免终点铁液温度过高。否则不但多耗电,还增加了降温时间。炉内静止降温很慢,3t 炉在无覆盖的情况下,每分钟降温不超过3℃。
(10)采用优质炉衬材料,延长炉龄。
(11)在保证炉龄的前提下,炉衬不宜过厚。因为壁厚增加会降低电效率和感应器的输入功率,降低了生产效率,而且由于不易形成良好的初期烧结层,致使初期熔蚀加快。坩埚壁厚与炉子容量及坩埚直径的关系见表1。
注:d 为坩埚的平均直径。
(12)合理的坩埚绝热层厚度。为了减少坩埚壁的散热,需要一定厚度的绝热层。但绝热层增厚时,绝热层内侧温度上升,会使烧结层或半烧结层扩展而缩小松散层。一般绝热层厚度取5~7 mm。一旦要增加绝热层时,捣打料中的胶结剂加入量应减少。
(13)调度上要避免感应炉被迫等待造型的情况。
(14)熔炼工部天车配置要合理,防止熔炉等天车而造成窝工。在采取以上种种措施后,先进的指标可达到:电耗580~540 kW/t;连续熔化,冷料至1500℃铁液的熔炼时间为35~54 min/炉。
5 减少事故的措施
感应炉熔炼过程中出现的事故和问题,大多来自感应炉系统(中频电源及炉子)和炉台操作。好的感应炉系统可以免除许多烦恼,减少维修费用和停工损失。
5.1 正确配置感应炉系统
国内多家公司生产的感应炉已相当完善,达到无故障设备的水平。因此,有相当规模的铸造企业应从这些公司中寻找供货商,它们会提出详细的项目书。该感应炉系统对电源、炉体、倾炉系统和水冷系统等进行显示、报警、诊断和故障处理。根据炉内变化着的情况,变频器会处于高效运行状态。一个高度自动化的感应炉,人工操作仅限于接通电源、开启变频器和调定输入功率,无需设专人看守变频器或作其他操作调节。如果铸造企业受生产量和经济条件所限,在感应炉技术改造时,应听取行业组织和专家的建议,并向供应商重点了解几种情况:①所用可控硅、控制板、集成块、元器件、绝缘材料以及液压缸、水泵、冷却设备等辅机的来源和配套情况;②配件库的状况;③服务能力和响应速度。
笔者发现,有铸造厂喜欢就近就熟(熟人)购买“便宜货”。这些供应商主要生产炉子,其余是“串起来”的。而且2t 炉还用铝壳。试想,这样的系统可靠性、耐用性会是怎样?按照国家发改委铲业结构调整指导目录(2011 年本)》规定,无磁轭(≥0.25 t)铝壳炉属于淘汰类产品。用铝壳炉也有违工信部《铸造行业准入条件》中,关于企业生产装备的要求的。
5.2 正确进行炉台操作
炉台操作不当,容易造成炉料搭棚,炉底熔池过热,“大象脚”和漏底等事故。这些事故多与炉料尺寸过大、野蛮装料、炉衬材料及烧结工艺不当、铁液过热温度过高,以及炉衬修补不及时等有关。企业管理者,不能把炉台操作看作体力活,一定要加强岗位培训,提高员工素质。
耐火材料的生产公司很多,著名的公司都有很好的服务,如推荐适用的耐火材料及辅料,指导筑炉和炉衬烧结,并对最低炉衬使用寿命做出保证等。
5.3 及时的信息测报
对铁液的化学成分和凝固信息要作炉前测报,以便及时指导生产,防止铸件质量事故。直读光谱仪的标准曲线,过一段时间应重新做,这是因为曲线会漂移,而且国产标样,其深层成分与浅层成分也会有所不同。热分析仪也应该定期校验。化学分析法虽然慢,用作炉后分析,准确性高。C、S、P、Mg 等对光谱分析操作手法很敏感,应该用化学分析的结果进行比照。
(摘自:《铸造》)
附件下载:

-
地址:济南市解放路134号 电话:0531-86401781 / 86952422 传真:0531-86465075
邮箱:foundry-shandong@163.com 邮编:250013
版权所有 © 山东省铸造协会 鲁ICP备2021002429号
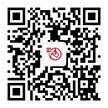
官方公众号