会员登录
MEMBER LOGIN
技术论坛
TECHNOLOGY FORUM
6MW 风力发电机组主机架、轮毂铸件的研发和生产
发布时间:
2013-05-28 00:00
来源:
(浙江佳力风能技术有限公司,浙江杭州311241)
摘要:6MW 风力发电机组主机架、轮毂铸件重达50 多吨,属于特大型厚壁高韧性球墨铸铁件。本文分析了6MW 主机架、轮毂生产的技术难点,提出了解决方案,介绍了主机架和轮毂的铸造工艺和生产情况,经理化检验和无损检验等,铸件的各项技术指标完全达到相关技术规范的要求。
关键词:特大型铸件;高韧性球墨铸铁;厚大断面球墨铸铁件;铸造工艺
1 前言
近年来,风力发电在我国呈现出跳跃式的发展。据初步统计,2011 年,我国新增风电装机容量接近1800 万千瓦,总装机容量达到6500 万千瓦,已是世界上风电设备制造大国和风电装机容量最多的国家,成为名副其实的风电大国。随着陆地风场的不断开发,我国又吹响了开发海上风电的进军号,国内多家风电主机制造骨干企业都开始了海上风电机组的设计和生产。2011 年,我公司承接了一套6WM 风力发电机组主机架、轮毂铸件的生产订单,为国内某风电主机制造骨干企业的海上风电机组的样机而生产的。这是我国制造的第一台6MW风力发电机组。
6MW 主机架和轮毂的立体图分别见图1 和图2。主机架铸件重量58.48t,铸件轮廓尺寸长5450mm、宽5400mm、高4580mm,铸件主要壁厚100~120mm,最小壁厚90mm,最大截面厚度320mm;轮毂铸件重量50.87t,轮廓尺寸长4485mm、宽3870mm、高4070mm,铸件主要壁厚80mm,最小壁厚66mm,最大壁厚330mm。6MW 主机架、轮毂铸件按照国家标准与欧盟标准设计、制造。其材料是牌号为QT400-18AL 的高韧性球墨铸铁,除了要求有良好的抗拉强度、屈服强度以及较高的伸长率外,还要求有良好的低温冲击韧性。对铸件的金相组织也有很高的要求,不但要检查附铸试块的金相组织,还要检查铸件本体的金相组织,要求球化率不低于3 级,铁素体含量不低于90%,石墨大小4~6 级。除了理化检验之外,还要对铸件进行磁粉探伤、超声波探伤等无损检测,对铸件的内在质量、外观质量以及壁厚尺寸等均有严格的要求。相关的验收标准是,铸件尺寸公差按照ISO8062 CT12;超声波探伤按照:EN12680-3,2 级;磁粉探伤按照EN1369,2~3 级。
6MW 主机架、轮毂重量大,壁厚尺寸厚,形线复杂,属于特大型球墨铸铁件,生产的技术难度较大。比如,主机架的平均壁厚约160mm,最大壁厚约400mm,是典型的厚大断面球墨铸铁件。生产厚大断面球铁件常常出现石墨漂浮、石墨开花、碎块状石墨,以及石墨球数少、石墨尺寸大等问题。这些都直接影响到材料的力学性能,特别是低温冲击
性能。从铸造工艺方面看,必须设计出适合的浇注系统和补缩系统,使铁液充型平稳、快速,铸件凝固均衡,补缩良好,防止铸件出现冲砂、夹渣、缩孔、缩松等铸造缺陷,获得健全的铸件,保证铸件的内在质量和外观质量能够通过超声波探伤和磁粉探伤的检查。这需要解决很多技术难题。
2 生产工艺和主要生产设备
采用树脂砂铸造和电炉熔炼来生产6MW 主机架、轮毂。主要铸造设备有l00t/h、60t/h连续式树脂砂混砂机各一台,7mx 8m、7mx 6m 振实台各一台,lOOt、80t、50t 行车各一台,20t 一拖二中频感应电炉一台,30t 电动铁水包2 个、20t 电动铁水包1 个。
3 技术难点和解决方案
3.1 熔炼工艺
厚大断面球铁铸件在浇注之后的冷却凝固过程中,由于铸件的壁厚尺寸大,冷却速度缓慢,凝固时间长,在铸件中容易出现球化衰退、石墨漂浮、石墨开花、石墨球数少、石墨尺寸大、碎块状石墨等问题。
一般认为,重稀土与轻稀土相比较,重稀土的抗球化衰退的作用更强,故提倡用钇基重稀土球化剂来生产厚大断面球墨铸铁件。但对此也有不同的意见,认为在1300℃以下,重稀土的抗球化衰退作用并不比轻稀土强。我们决定采用经验的做法,按照一定的比例,将重稀土和轻稀土的球化剂复合使用,来生产6MW 主机架和轮毂。
防止石墨漂浮的主要措施是控制好碳当量。风电球墨铸铁件,既风电铸件的碳当量一般控制在4.30%~4.50%,考虑到6MW 主机架和轮毂的壁厚特别厚大,应当将碳当量控制在4.30%左右。
尽管通常认为石墨开花(或爆裂状石墨)是伴随着石墨漂浮产生的,但在实际的金相检验中会看到有石墨开花,却并不伴随石墨漂浮,我们更愿意将石墨开花归入石墨畸变一类的缺陷之中。石墨畸变是厚大断面球铁中最常见、最难避免的一种缺陷。由于石墨球化理论的不完善,导致石墨畸变的机理也无定论。尽管如此,还是有一些行之有效的方法应用于球墨铸铁的生产之中,来解决石墨畸变的问题。抑制石墨畸变的措施主要有对原铁水进行脱硫处理,以减少球化剂的用量。将稀土和镁含量控制在相对较低的水平;在铸件的厚壁处使用冷铁等激冷物,增加铸件的冷却速度;控制铸件的含硅量以及微量元素含量;加入少量Sn、Sb或Bi 等微量元素进行微合金化处理等。实践证明,以上措施的综合应用,可以有效防止厚大断面球墨铸铁出现石墨畸变,并增加石墨球数。石墨大小和石墨球数都会影响到球墨铸铁的力学性能,在生产风电铸件时要特别注意这两项金相分析指标。要增加石墨球数,减小石墨大小,首先可以采用预处理工艺;另一方面要做好孕育处理,采用具有不同特点的孕育剂(比如含Ba、Ca 的孕育剂,含S、O 的孕育剂)进行复合孕育处理,要重视随流孕育;再就是如前所述,用Sb、Bi 等微量元素进行微合金化处理。
3.2 铸造工艺
风电铸件一般采用底注式浇注系统。底注式浇注系统具有铁液充型平稳,氧化小,型腔排气顺畅等优点,但不利于铁液中的熔渣、砂粒等夹杂物上浮。充型后铸件上部的温度低于下部温度,不利于补缩,浇注时间较长、浇注温度过低的情况下容易在铸件上部出现氧化皮夹杂物等缺点。6MW 主机架、轮毂铸件的高度达4m 多,底注式浇注系统的缺点就更显突出。根据6MW 主机架和轮毂重量看,都需要采用2 套以上的独立浇注系统来进行浇注。这就可以将一套浇注系统采用底注式的,另一套浇注系统采用中注等其他方式。但存在一个问题,另一套浇注系统的注入位置不好确定。由于主机架和轮毂的特殊结构,除了底注之外,难于在铸件上另外再找到一个合适的注入位置,能够将铁液平稳地、均匀地引入型腔。经过分析,最后决定全部采用底注式浇注系统。对底注式浇注系统的不足之处,则采用其他办法来加以弥补。比如,适当的提高浇注温度和浇注速度,采用发热保温冒口来提高补缩效率等。6MW 主机架和轮毂要进行超声波无损检测,必须对铸件的缩孔、缩松缺陷进行严格的控制。首先,必须设计好铸件的补缩系统。为了提高补缩效率,取得良好的补缩效果,采用冷铁和冒口相结合的补缩系统。在铸件的厚大部位和一些机加工面设置冷铁,在铸件的顶面设置冒口。在设计补缩系统时,用计算机进行凝固模拟,根据凝固模拟的结果和经验来调整冒口、冷铁的大小和位置。
6MW 主机架和轮毂铸件的高度有4m 多,加上砂型和浇口盆的高度,整个铸型高达7m多,铁液的压头很高,容易发生胀砂、粘砂、跑火等铸造缺陷。为了防止这些铸造缺陷,需要适当增加型砂中树脂的加入量,以提高树脂砂的强度。在造型时使用振实台来紧实型砂,提高砂型的紧实度,使用锆英粉涂料,防止粘砂。由于主机架和轮毂的抬箱力都高达数百吨,除了采用常规的放置压铁、用螺栓紧固砂型的方法,还要用焊接圆钢和钢板,对砂箱的重要位置进行紧固和加固,以防止发生跑火。
3.3 其他方面的技术难点和解决方案
6MW 主机架和轮毂是在我公司刚刚竣工的年产6 万t 的新工厂生产的。当时,铸造设备还没有全部安装完成,设备能力略显不足,特别是熔炼设备能力严重不足。为了解决这个问题,决定采用多开箱造型的工艺方案,设计专用砂箱,避免行车起吊超重。在熔炼时,先将熔化好的铁液存放在铁水包中,并采用保温措施,再结合回炉加温铁液的方法,待所需要的铁液全部熔化和加温完毕,再同时进行球化处理。在生产之前,设计了几套熔化、保温和加温的方案,以及球化处理后到浇注完成的最短时间的方案,通过多次试验、确定了最佳方案。6MW 主机架和轮毂铸件的形线复杂,壁厚不均且尺寸要求严格。木模形状尺寸必须准确,制作难度较大。必须应用三维CAD 技术,用数控木工机床制作木模。
4 铸造工艺、生产情况和质量检验
4.1 主机架、轮毂的铸造工艺
6MW 主机架的铸造工艺简图,见图3。采用了3 套独立的底注式浇注系统,直浇道和内浇道采用陶瓷管。计算的浇注时间为154s,最小阻流截面积240cm2,浇注系统各组元的比例为Σ直:Σ阻:Σ横:Σ内:=1.5:1:2:1.6。在铸件的顶面设置4 个Φ230mm 的鸭嘴冒口和一个直径Φ300mm 的发热保温冒口,在铸件的机加工面和一些厚大断面部位放置冷铁,多开箱造型。6MW 轮毂的铸造工艺简图,见图4。采用了2 套独立的底注式浇注系统,直浇道采用陶瓷管,内浇道采用披缝式浇口。计算的浇注时间为140s,最小阻流截面积200cm2,浇注系统各组元的比例为Σ直:Σ阻:Σ横:Σ内:=1.13:1:2:1.5。在铸件的顶面设置3 个Φ300mm的发热保温冒口,并在机加工面和厚大断面处放置冷铁,多开箱造型。
4.2 熔炼工艺
用中频感应电炉进行熔炼。炉料采用国产高纯生铁、低碳钢废钢以及风电铸件的回炉料,用冲入法进行球化处理,孕育处理的方法采用包内孕育和随流孕育,并进行了预处理和微合金化。球化剂和孕育剂的化学成分见表1。6MW 主机架的浇注重量为85t,同时处理3 包球墨铸铁进行浇注。轮毂的浇注重量为64t,同时处理2 包球墨铸铁进行浇注。
4.3 生产情况和质量检验
经过生产现场测量,主机架的实际浇注时间为144s,三包铁液的浇注温度分别是1319℃、1320℃、1337℃;轮毂的实际浇注时间为125s,两包铁液的浇注温度分别是1318℃和1345℃。
主机架和轮毂铸件均在浇注之后冷却196h 以上开箱,开箱温度不大于300℃。最后,对6MW 主机架和轮毂铸件进行了形状尺寸检验、表面质量检验、超声波探伤、磁粉探伤、理化检验以及本体金相分析。力学性能试验是用厚70mm 的附铸试块制样进行试验的。所有的检验结果均达到技术规范的要求。其中,力学性能检测的结果见表2,附铸试块的金相分析照片和本体金相分析照片分别见图5—图8。金相照片的放大倍数均为100 倍。
5 结束语
厚大断面球墨铸件的生产一直存在许多难题。采用电炉熔炼,树脂砂铸造,底注式浇注系统,多开箱造型,将轻稀土和重稀土球化剂组合进行球化处理、复合孕育处理、预处理、微合金化等技术方法,成功生产出重达50 多吨的6MW 风力发电机组的主机架和轮毂球墨铸铁件。目前,主机厂已经完成了6MW 主机架和轮毂的组装,风力发电机组成功下线。
(摘自《2012 中国铸造活动周论文集》)
附件下载:

-
地址:济南市解放路134号 电话:0531-86401781 / 86952422 传真:0531-86465075
邮箱:foundry-shandong@163.com 邮编:250013
版权所有 © 山东省铸造协会 鲁ICP备2021002429号
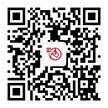
官方公众号